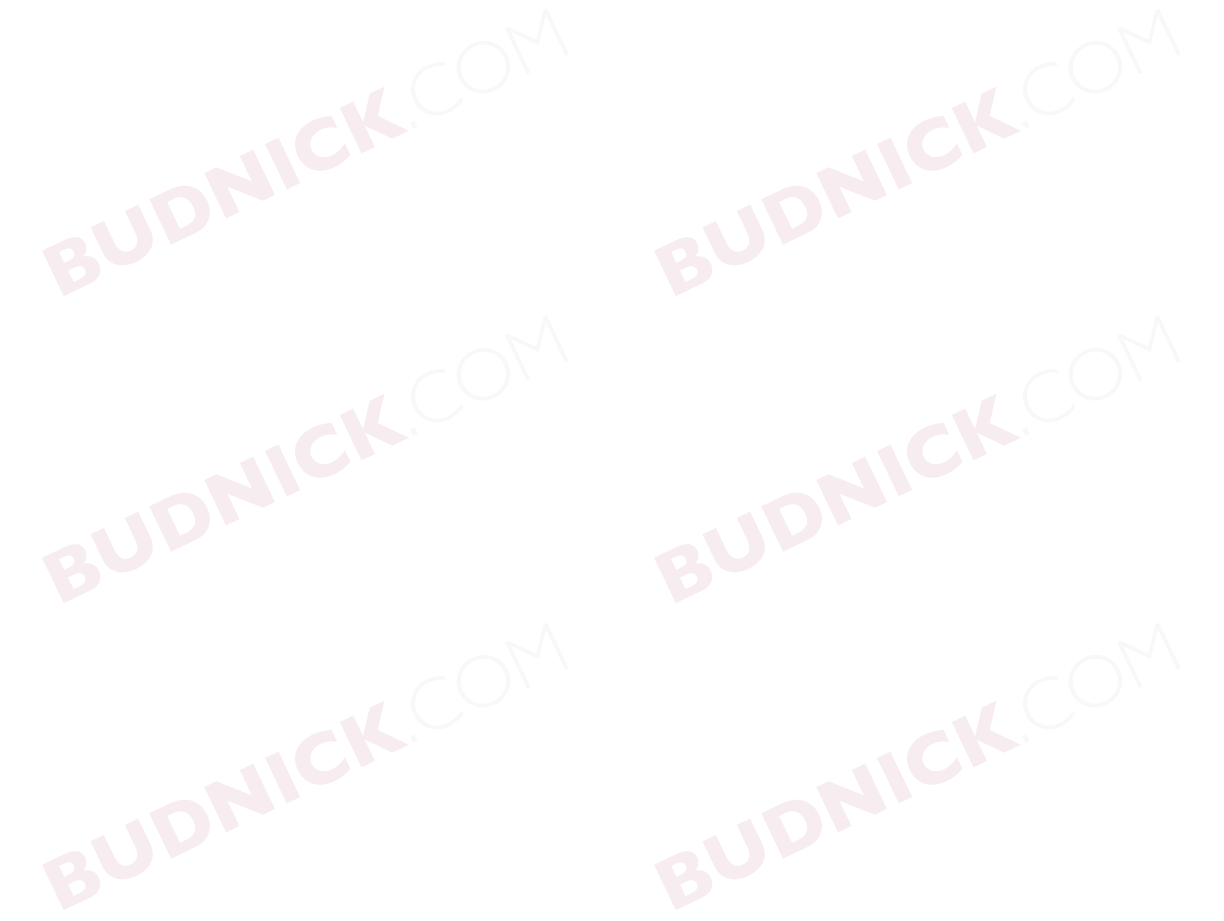
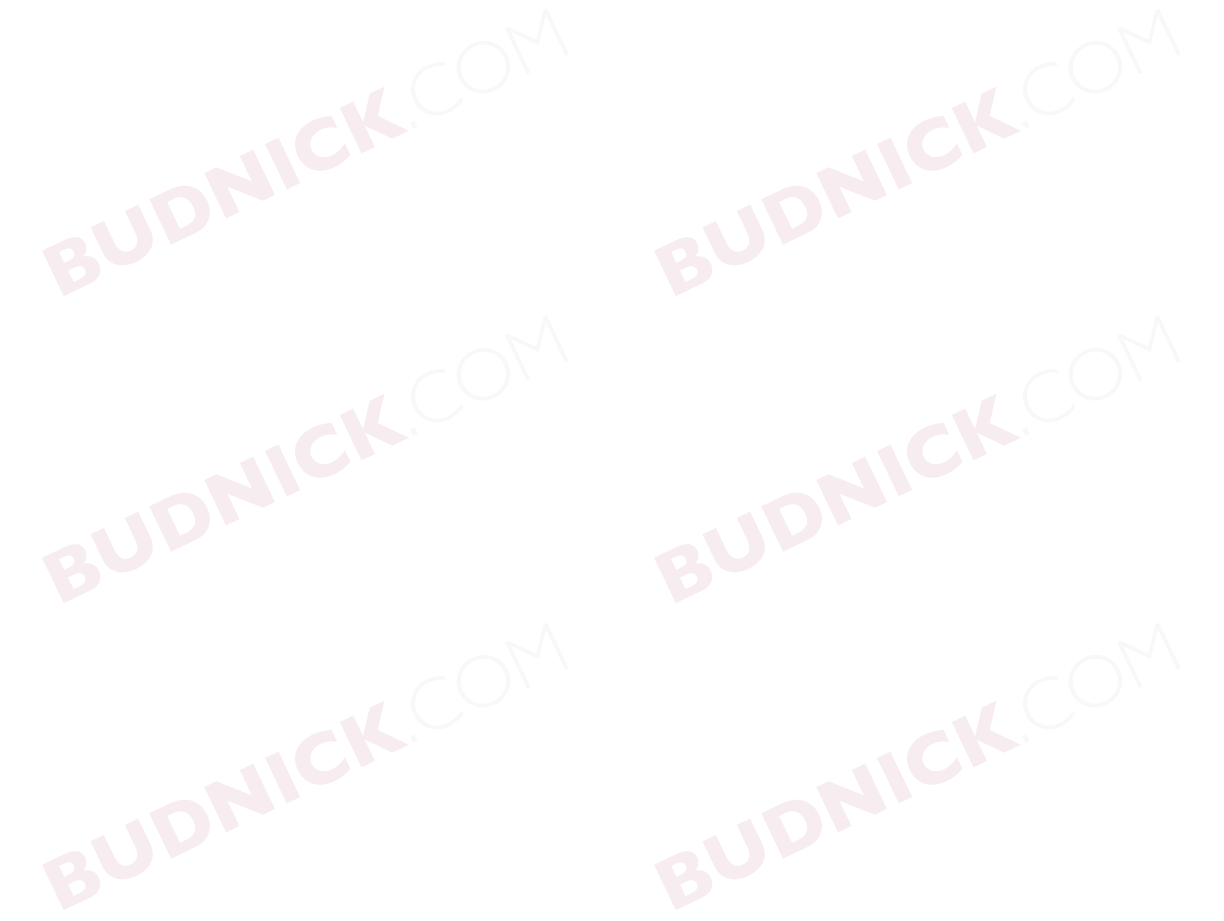
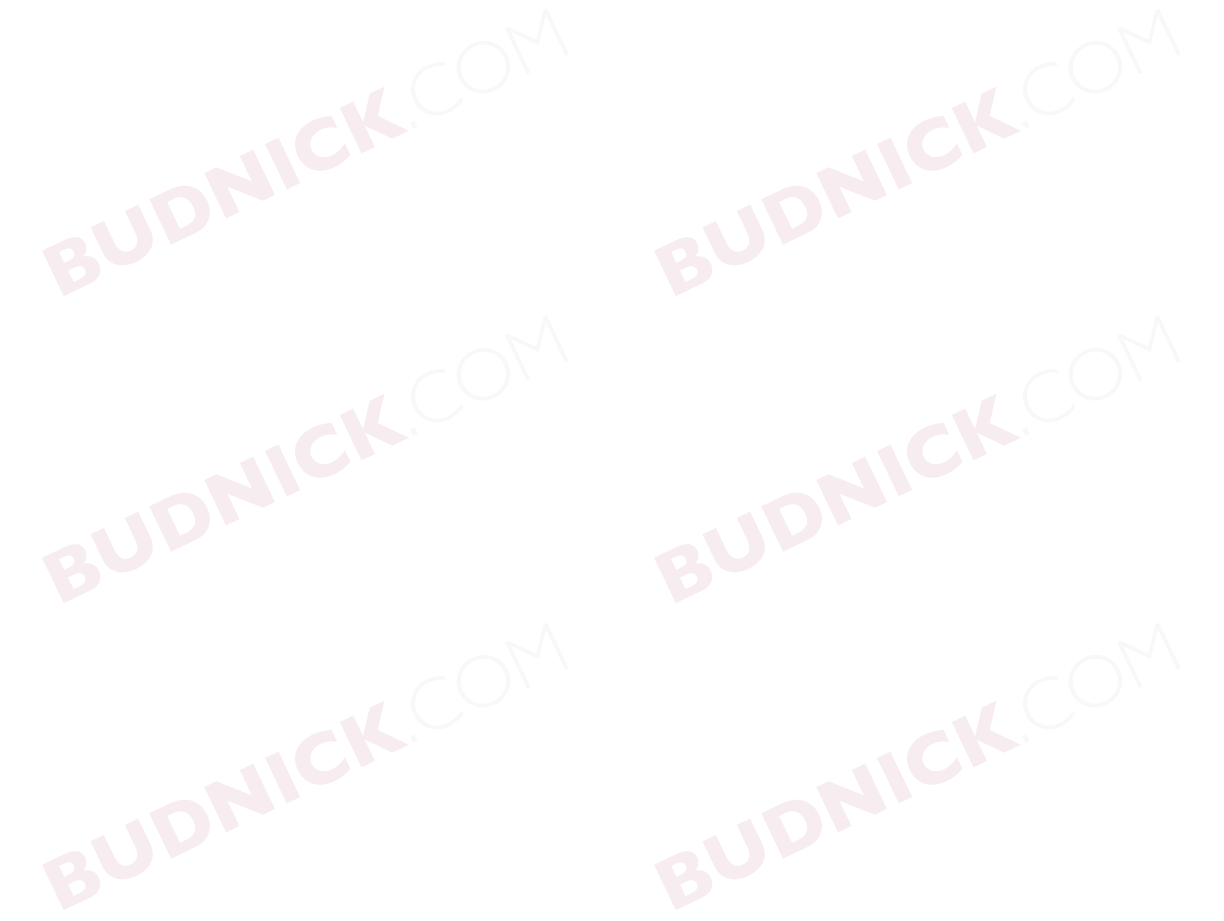
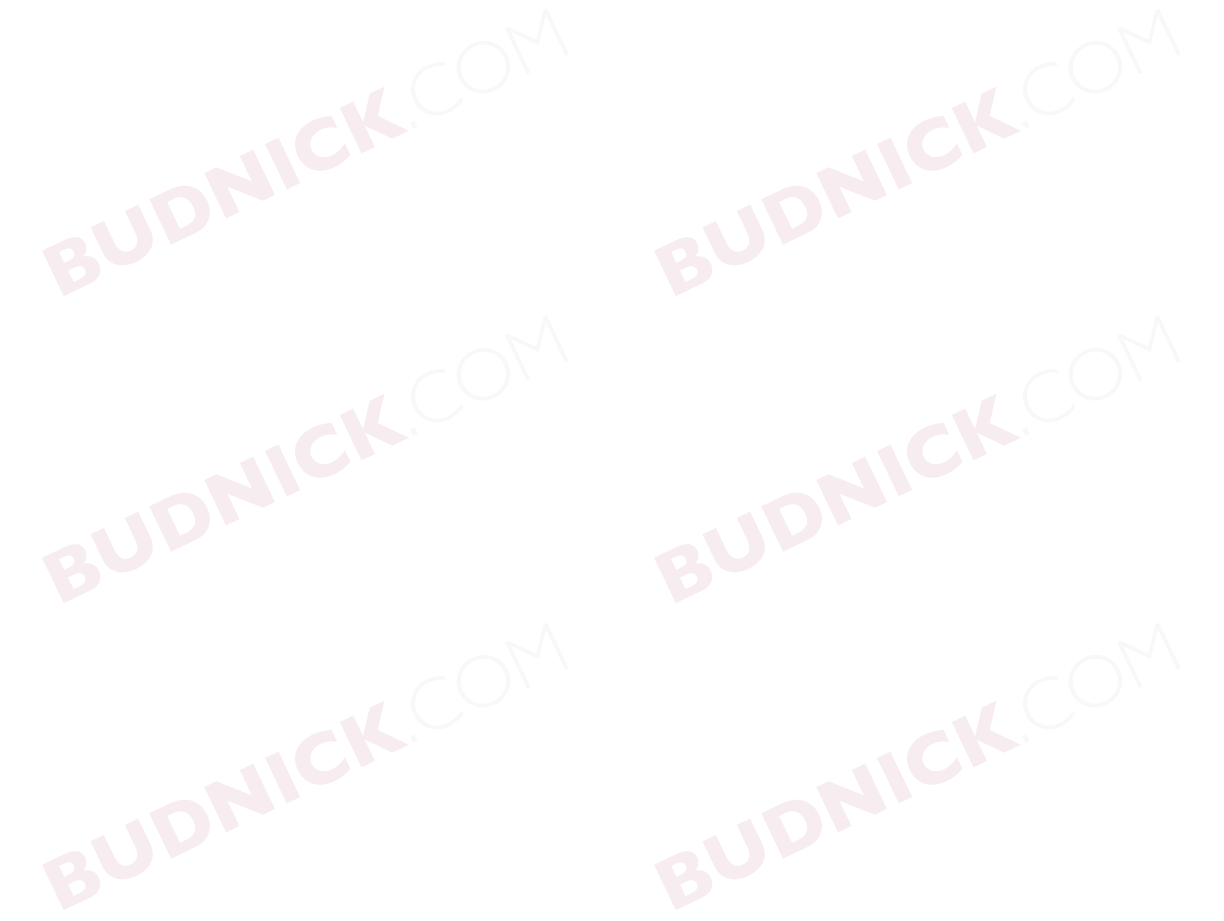
Exploring Elements of Adhesive Tapes: A Candid Look at Tape Backings
In today’s advanced information age, a common search for the term “Pressure Sensitive Tape” will likely result in a response similar to this:
Wikipedia, (the free encyclopedia) – The tape consists of a pressure-sensitive adhesive coated onto a backing material such as paper, plastic film, cloth, or metal foil. Some have a removable release liner which protects the adhesive until the liner is removed. Some have layers of adhesives, primers, easy release materials, filaments, printing, etc. made for specific functions.
Descriptions such as this, however, fail to capture the important role that each of these elements play with regard to today’s advanced pressure sensitive adhesive tapes. While all tape components are important when determining performance, this article will offer a closer look at the all-important tape backing systems.
![]() |
In years past, the main function of a tape backing, otherwise known as a “carrier,” was to “carry” the adhesive to its point of use. Today, tape backings are most often highly engineered and essential components of the overall tape solution. Today’s backings are designed to withstand certain forces or to split at an exact defined force; to be optically clear or reflective; to be permeable or to function as a barrier (e.g. for humidity or oxygen); to be very thin (1.5 μm = 0.059 mils) or to be very thick(>3mm or 118 mils); to serve as gap fillers and/or noise dampers; and to enable the tape to be machine-processed and/or die-cut. These functions are merely a few examples of the variety of functions modern tape backings can fulfill. Due to the multiplicity of the available types of backings, it is worthwhile to discuss features and benefits of the different types |
Paper Backings
Paper backings are mainly used for masking applications.They are easy to tear by hand; allow for good conformability to a variety of surfaces; offer good temperature and solvent resistance; and they are environmentally compatible. Higher degrees of “crepe” to the paper allows for easier application of the tape to curves and contours. It is important that the paper be paintable, otherwise the paint would not stick to the backing, and there is the risk that recently painted areas would be unintentionally contaminated. There are more complex paper backings which are used in the paper industry for splicing or end tabbing large paper rolls. In this application, the paper needs to be repulpable (dissolvable without leaving any residues in the newly produced paper).
Filmic Backings
The most used filmic backings are; Polyvinyl Chloride (PVC),Polyethylene (PE), Polypropylene (PP), and Polyethylene Terephthalate (PET). Let’s take a closer look at each type.
PVC
Generally speaking, PVC backings typically exude the following characteristics: durability, low flammability, printable, can be embossed, weather resistant albeit temperature sensitive. PVC can be produced in both rigid and soft configurations. Rigid PVC is mainly used as the backing of choice for carton sealing tapes. Soft PVC is most often used as backing for insulating tapes and masking tapes, allowing for the flexibility of applying to curves and contours.
PE, PP
These two backings – Polyethylene and Polypropylene – are the environmentally friendly alternatives to PVC. PE offers low cost, good flexibility, and due to its softness, a high conformability. PP is a mono-axial-oriented film (MoPP), meaning that it supplies strength in only one direction, as compared to bi-axially-oriented film (BoPP) that offers strength in two directions, along with other various advantages. MoPP shows very high tensile strength (in mid-direction) and low elongation (in mid-direction), but also low tensile strength in cross direction. This makes the backing ideal for strapping and bundling applications, as well as for packaging applications that utilize tear strips. BoPP backings offer low-cost, high tear resistance in mid-direction and cross direction, extreme flatness, and well-balanced mechanical properties.
PET
Polyester backings are mostly used as BoPET (bi-axiallyoriented polyester). PET is available in a very wide range of thicknesses (1.5 μm to 500 μm/0.059 mils – 19.68 mils). The advantages of polyester include high-temperature resistance and high UV stability. It is the preferred backing for die-cutting processes, and therefore, it is one of the most commonly used backings in the PSA industry.
Foam Backings
In addition to performing the function of bonding two parts together, PE foam tapes are often used for a variety of reasons: to fill gaps/space between the bonding parts; to compensate for design intolerances; to be conformable to irregular surfaces; to offer very high bonding strength to compensate for different thermal expansions; and to work as a damping element, as well as a shock absorber. Application examples for foam tapes are endless; specific examples include bonding plastic emblems onto metal substrates (Automotive Industry), or bonding muntin bars on windows, or in many other high-end applications. In Flexographic printing applications, the foam tape not only holds the printing plate onto printing cylinders/sleeves, but also defines the print quality by its hardness/softness level, as well as altering the possible printing speed by its elasticity and recovery (memory) rate. The faster the foam recovers, the higher the possible printing speed. Additionally, since some print jobs are very long, the foam performance must maintain its stability throughout thousands of impressions. Closed-cell PE foams have proven to be very suitable for most applications. As Polyethylene has a low melting temperature, the application for PE foams is limited to temperatures below 200°F.
Acrylic Core Backings
For high temperature applications (above 200°F), or for applications that require even higher performance than a foam tape can offer, acrylic core backings are the high-end solution. Due to the fact that the backing is made of an acrylic polymer, the backing has outstanding visco-elastic characteristics. In simple terms, the backing is able to dissipate stress, which leads to a much higher performance than “normal” backings. Additionally, the visco-elastic property of the acrylic core backing is capable of compensating for different thermal expansions in a much higher degree than a PE foam tape. Evaluations have shown that depending on the backing structure, the thermal compensation can achieve three times the thickness of the tape. Combined with the very high bonding strength, acrylic core tapes are the ideal solution for bonding differing substrates such as glass to metal, or metal to plastic. As an added benefit, acrylic backings are very resistant to many environmental elements, such as sunlight, ozone, temperature, and water. These characteristics make acrylic core tapes the ideal choice for long-lasting, high-performance outdoor applications. Application examples include bonding body side moldings to car bodies (automotive); bonding framing of flat screens (electronics); bonding glass panels to metal frames; or joining photovoltaic panels onto back rails (solar panels). These and other appropriate applications demand high-bonding strength, long-term (up to 25 years) outdoor performance, and compensation of thermal differences.
In conclusion, when specifying your next adhesive tape application, take the tape backing’s features and characteristics into account. A good backing choice can put you in front of the competition.