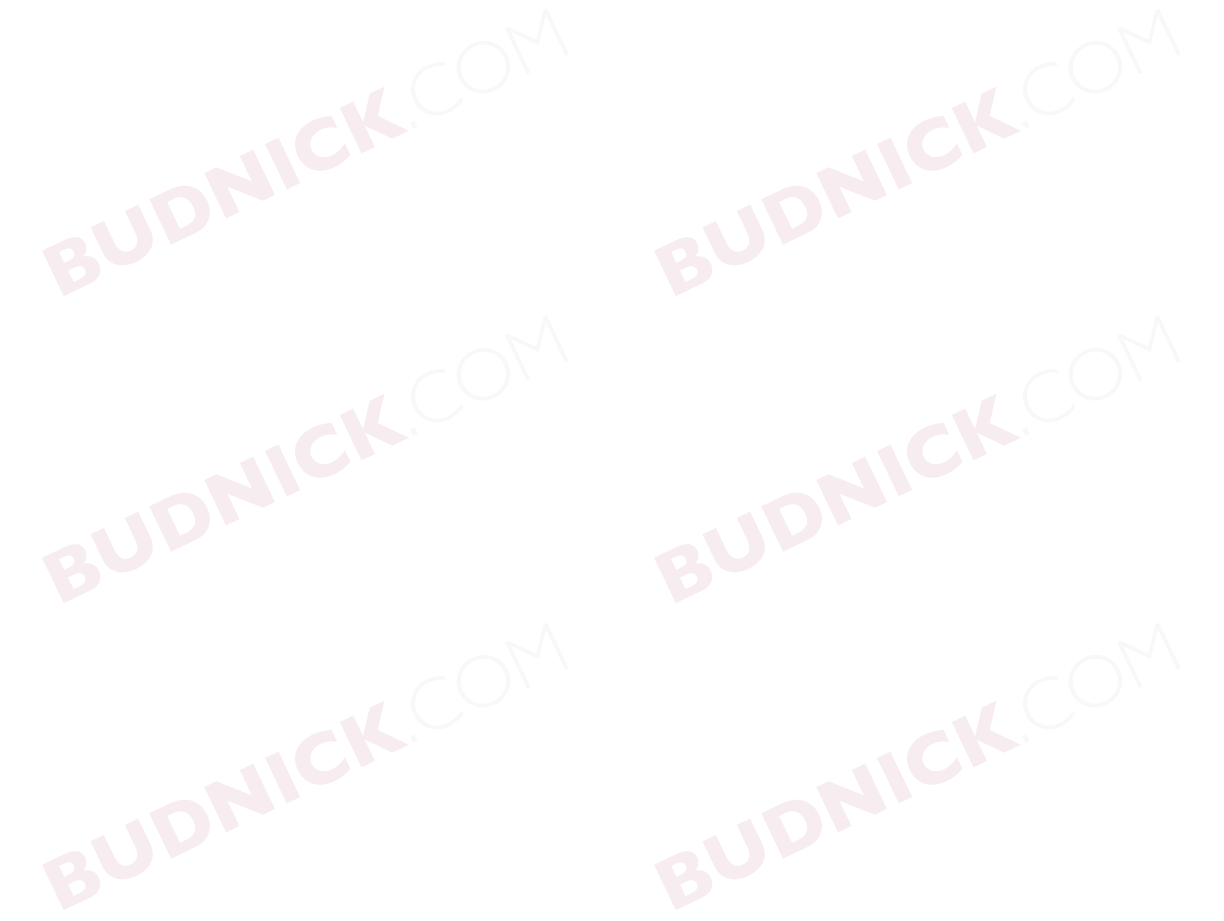
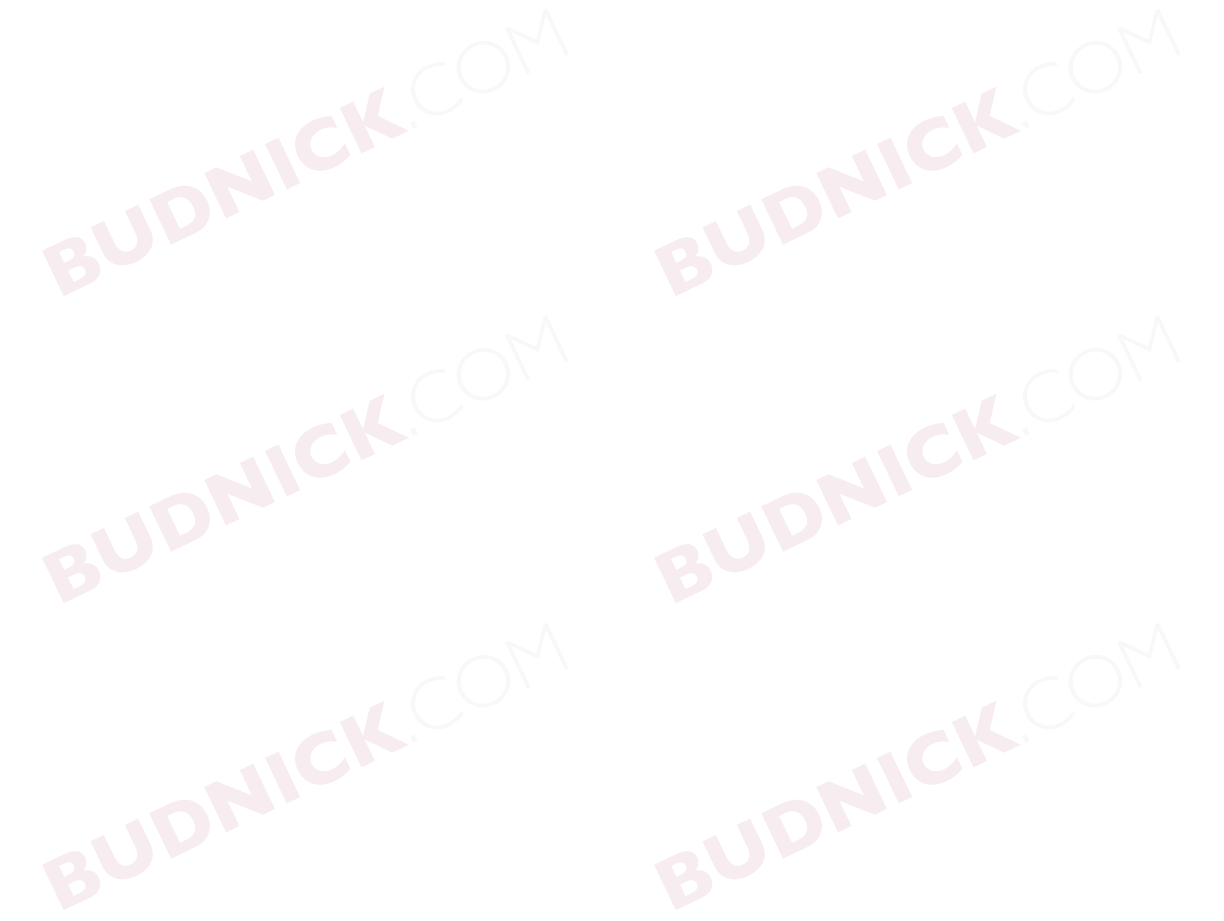
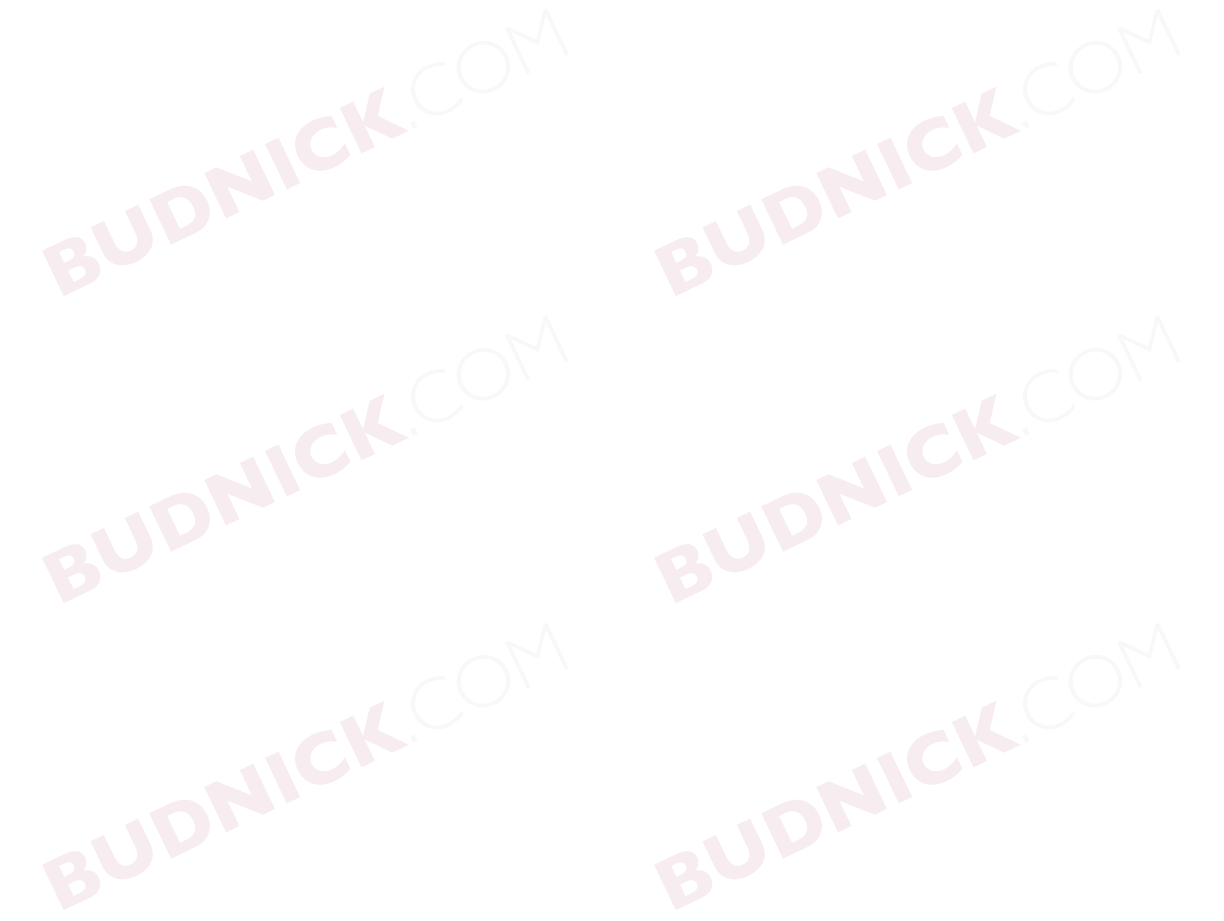
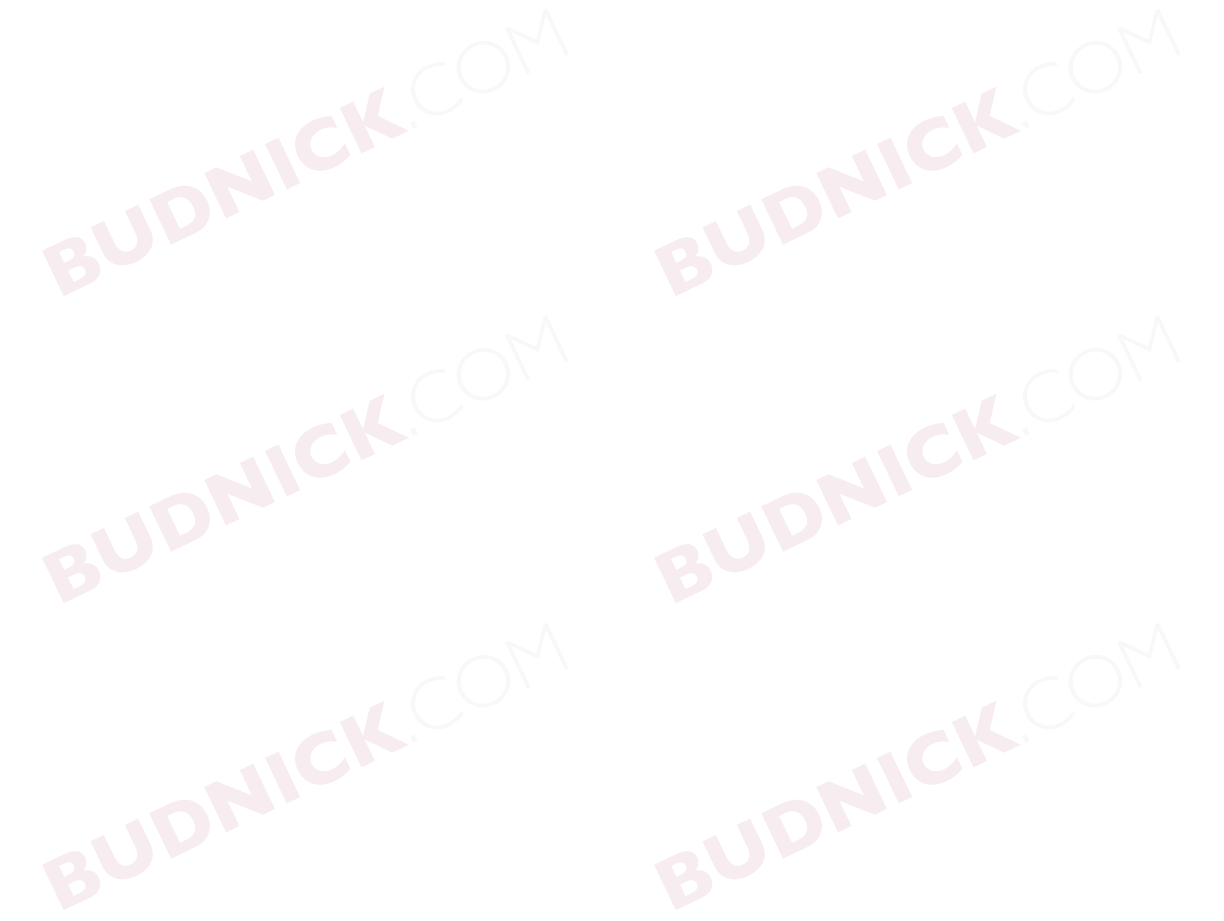
Case Study - Extrusion Attachment
Customer Need
Budnick was approached by a medical equipment manufacturer who was experiencing issues with an extrusion that was being attached to a medical sink. The customer was using a double coated structural foam tape provided to them by the extrusion manufacturer. The extrusion is designed to contain washing solution inside lids, without any splashing out. However, the tape was not adhering when applied to the sink basin. The customer was hoping to increase their production to forty units per week but were at a standstill due to the failing extrusion attachment.
The Budnick Solution
We initially recommended testing a high adhesion acrylic foam. The acrylic foam has quick-stick properties and is more pliable to fit the sink basin lin. After testing the foam, the customer gave the approval. Attention was then turned to the extrusion itself. The extrusion did not fit the track on the molded sink basin.
After asking the customer if they were open to redesigning the extrusion, we reached out to an extruder that was less than ten miles from the customer. We introduced the extruded to the sink manufacturer and a new extrusion was developed.
Creating Value for Our Customers
Since sourcing extruder for the customer, they have achieved their production goals of producing forty sinks per week. Additionally, we are currently working on future projects, duplicating some of the previously achieved processes.
Budnick’s tape specialists go to work for their customers to ensure they are using the optimal materials, from reliable partners to achieve efficiencies.