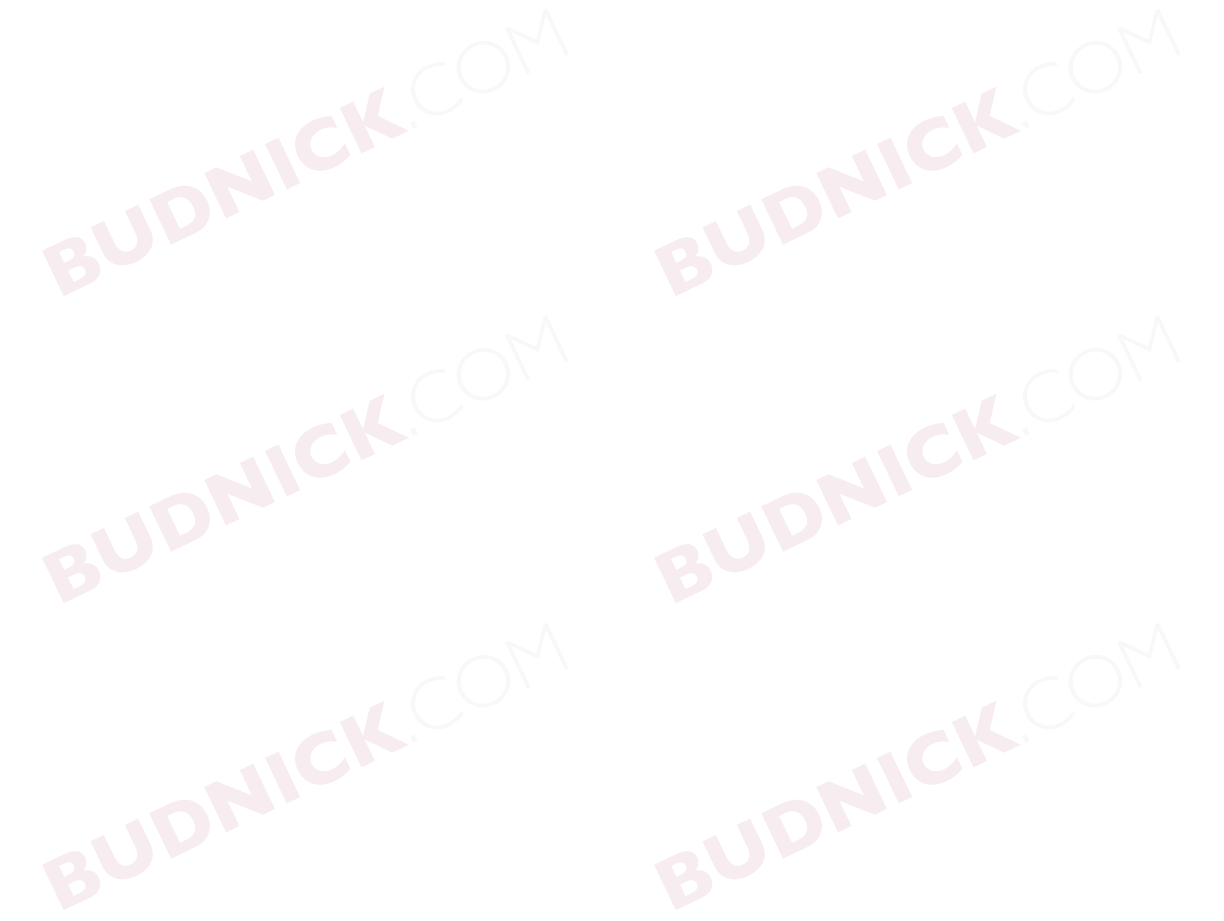
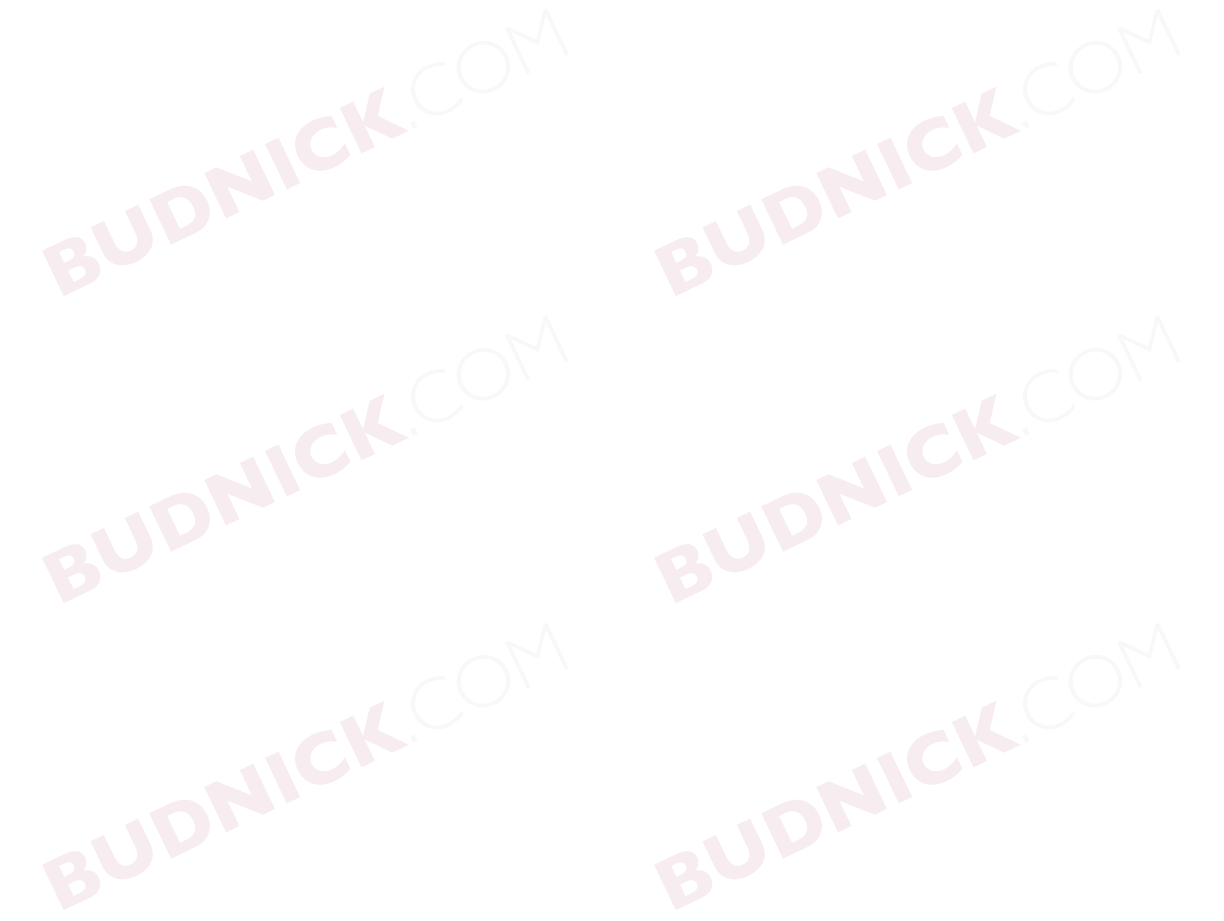
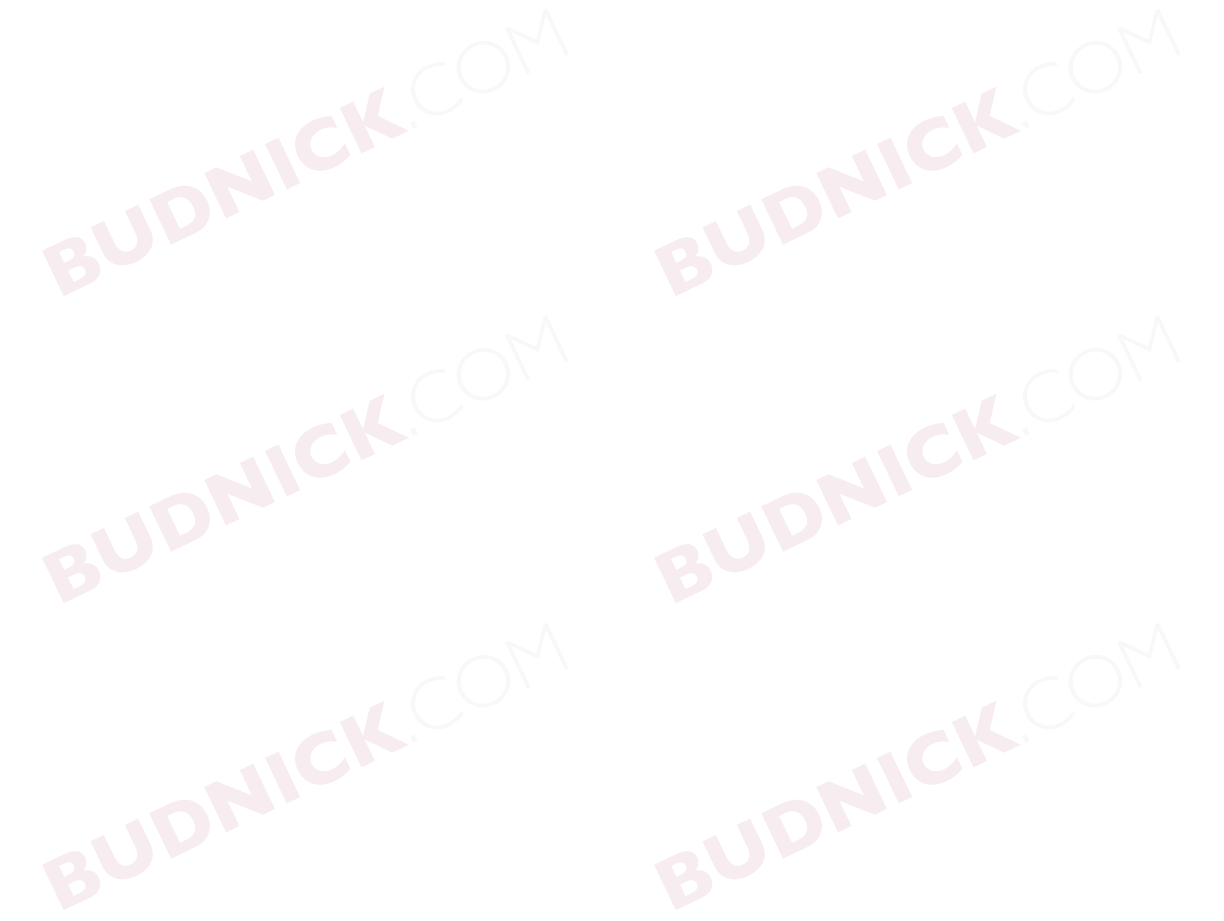
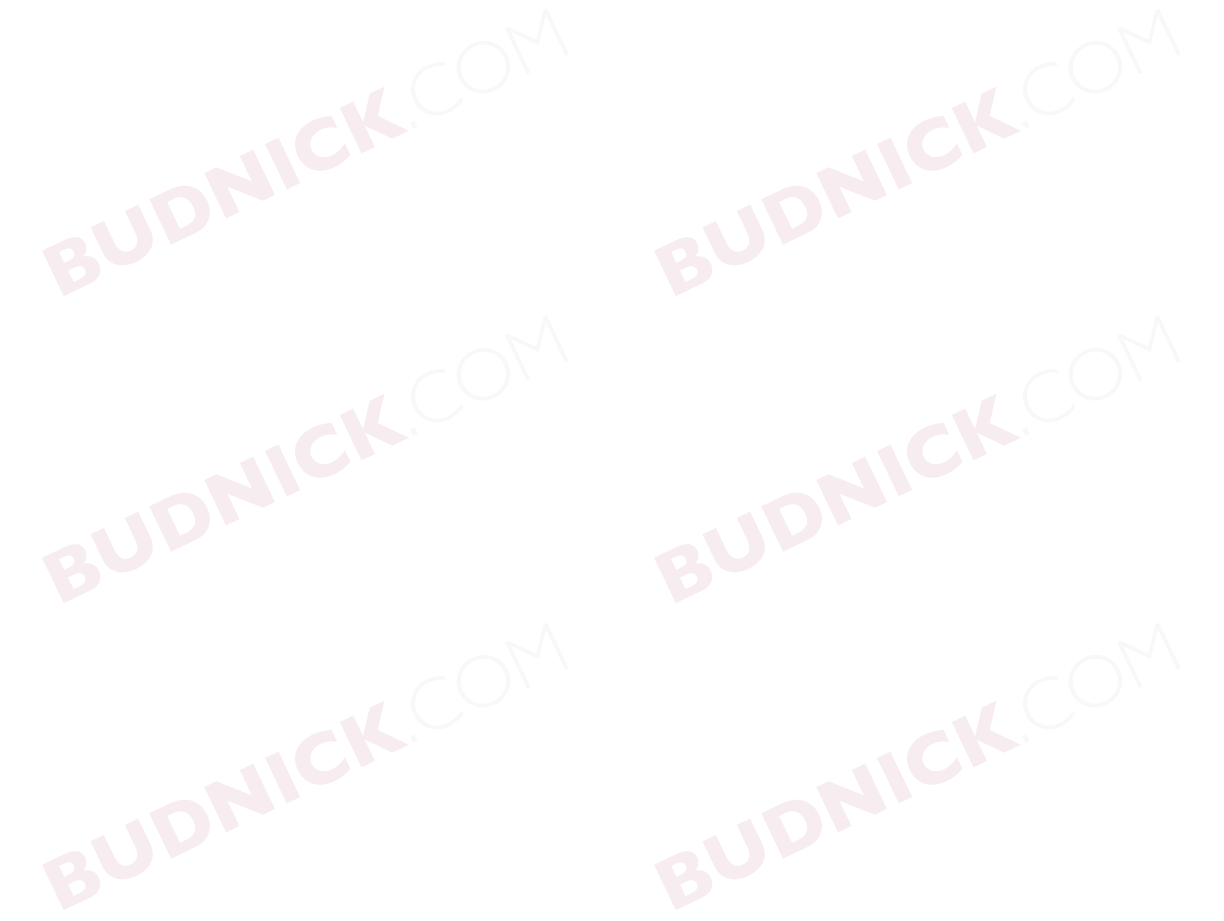
Medical
Budnick is an FDA Registered contract manufacturer, providing a full array of innovative adhesive and converting services to medical device manufacturers. Manufacturers benefit from Budnick’s prototyping capabilities, application engineering services, and strict ISO Quality Standards. Budnick sources products from almost every major manufacturer, providing a full selection of adhesive tapes, foams, and other materials.
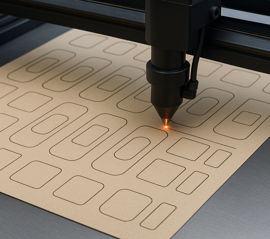
An ISO 9001:2015 Certified & FDA Registered Converter
Lot traceability and consistent production procedures are essential in maintaining the tight tolerances required of medical device manufacturers.
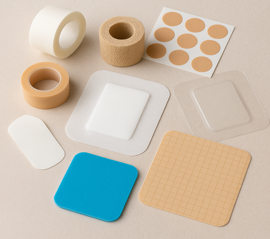
Material Sourcing
Working with a broad range of adhesive manufacturers, Budnick can source materials to meet the unique demands of medical applications, including biocompatibility, sterilizability, breathability, and skin-friendly adhesion.
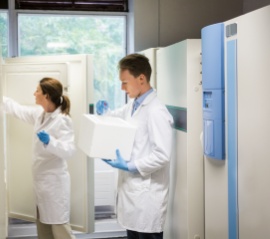
Medical Appliances
Budnick helps medical appliance manufacturers solve applications including bonding and mounting, foaming/venting/hole covering, seaming, gasketing, moisture control, sound damping, transportation, surface protection, and more.
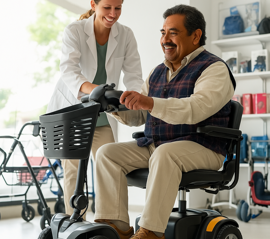
Durable Medical Equipment
High-performance adhesive solutions for bonding, mounting, cushioning, and sealing applications. From mobility aids to portable oxygen machines, we supply precision-cut tapes, foams, and specialty materials that ensure long-lasting reliability and patient comfort.
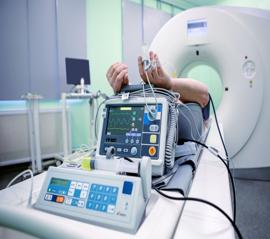
Electronic Devices
Budnick provides precision die-cut components, EMI/RFI shielding materials, thermal management materials, bonding & joining solutions, and more for medical electronic devices, supporting the growing demand for smarter, more connected healthcare.
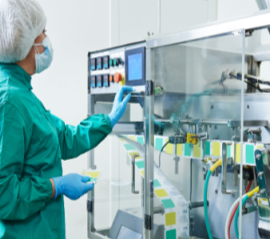
Pharmaceutical and Packaging
Adhesive materials and tamper-evident tapes for pharmaceutical packaging, medical labeling, and product security. Whether it's sealing medication packs, creating clean-release liners, or enhancing packaging efficiency, Budnick supports pharmaceutical companies with compliant and reliable adhesive solutions.
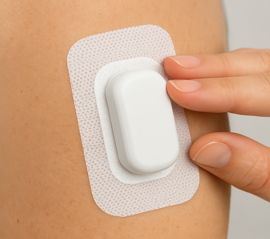
Wearables and Stick-to-Skin
Medical-grade adhesives for wearables, sensors, and transdermal patches that adhere comfortably to skin. We source breathable, hypoallergenic, and repositionable materials for applications ranging from remote patient monitoring to drug delivery.
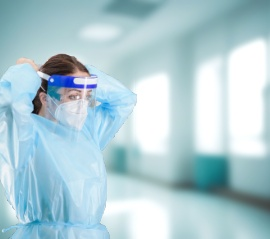
Woundcare, Disposables, and PPE
Adhesive and converted solutions for dressings, surgical drapes, bandages, device fixation, cosmetics, face shields, safety barriers, surface protection films, 95kPa and biohazard bags, hospital partitions, floor marking tape, and more.
We Provide Solutions for
-
- Inefficient Production Processes
- Air, Water, Moisture Intrusion
- Bonding & Mounting
- Attaching & Holding
- Lightweighting
- Skin Trauma/Stick to Skin
- Long Term Wear
- Aesthetics Issues
- EMI/RFI Shielding
- Electrical Insulation & Conductivity
- Thermal Management
- Reducing Component Size
- Electronic Bonding & Display Enhancement
To learn more about the solutions we provide, or to get started on a new project, contact us or click here to fill out an RFQ.
Case Studies
Budnick has combined our expertise in execution with a number of adhesive tape manufacturers to provide the world's best products for medical device manufacturers.
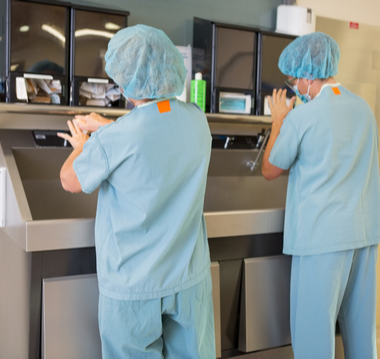
Case Study Extrusion Mounting
Unable to meet production goals due to an extrusion that failed to bond to a medical sink, this medical equipment manufacturer turned to Budnick to develop a solution.
- Customer was using an extruder’s failing foam to attach an extrusion to a sink base
- A new acrylic foam with quick-stick properties was tested and implemented
- Budnick worked with a new extruder to develop a properly fitting extrusion
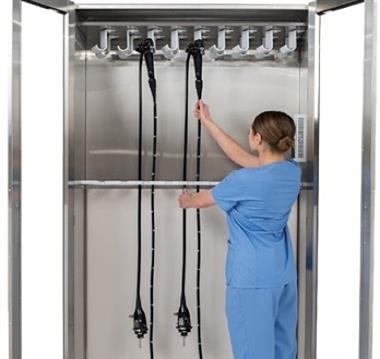
Case Study Reengineering
A medical equipment manufacturer turned to Budnick to implement process improvements related to their medical cabinets.
- Customer also wanted to reduce their number of vendors
- Customer needed a solution to mount brackets and secure a medical hose
- Both gaskets needed to be FDA approved due to cleaning and sterilization
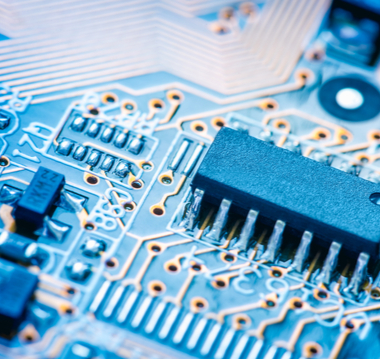
Case Study Reposition Thermal Interface
Finding a repositionable tape that bonds to silicone without interfering with thermal conductivity put Budnick’s tape experts to the test.
- Typically, silicone only bonds to silicone, but silicone tapes affected thermal conductivity
- Sufficient amount of testing took place before finding an acrylic transfer
- The acrylic adhesive did not prevent the heat transferring through the interface