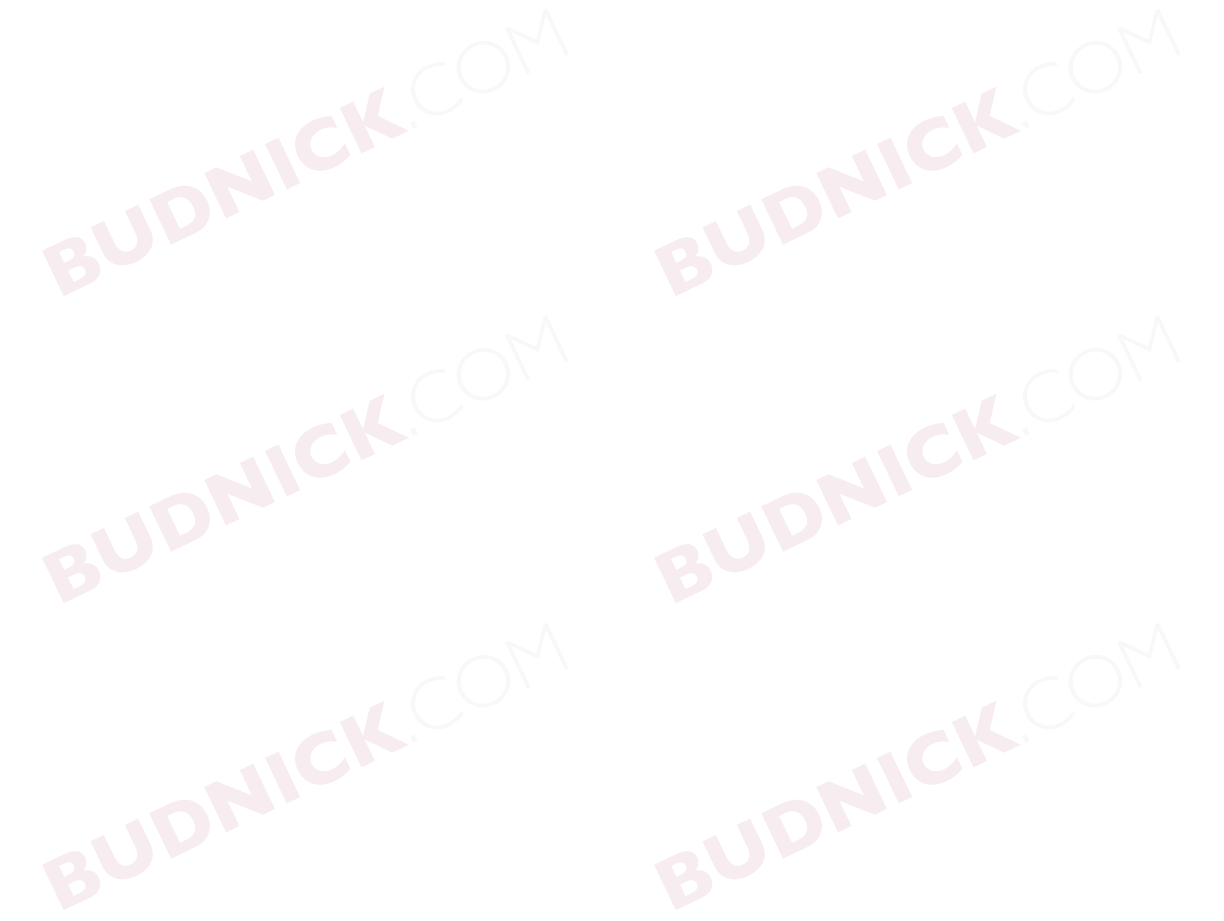
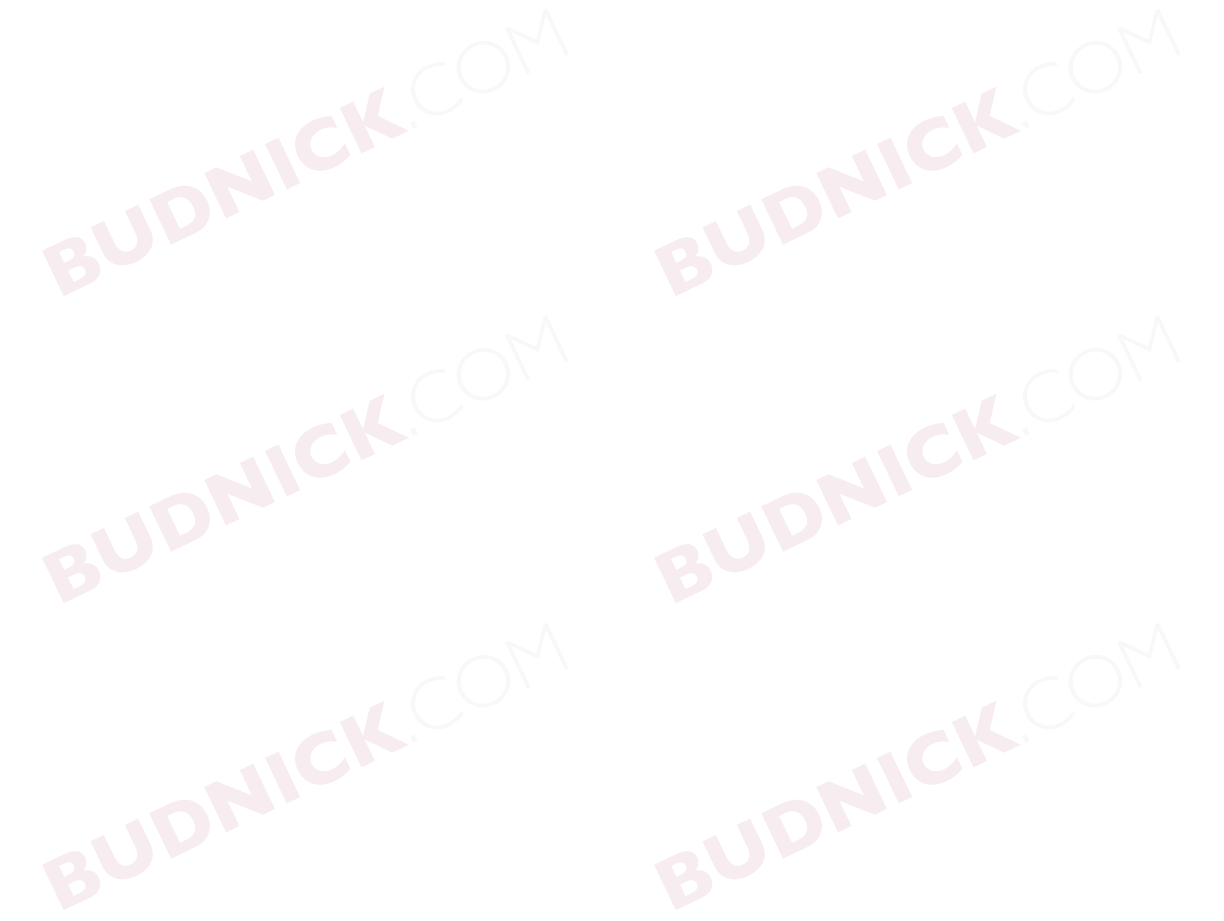
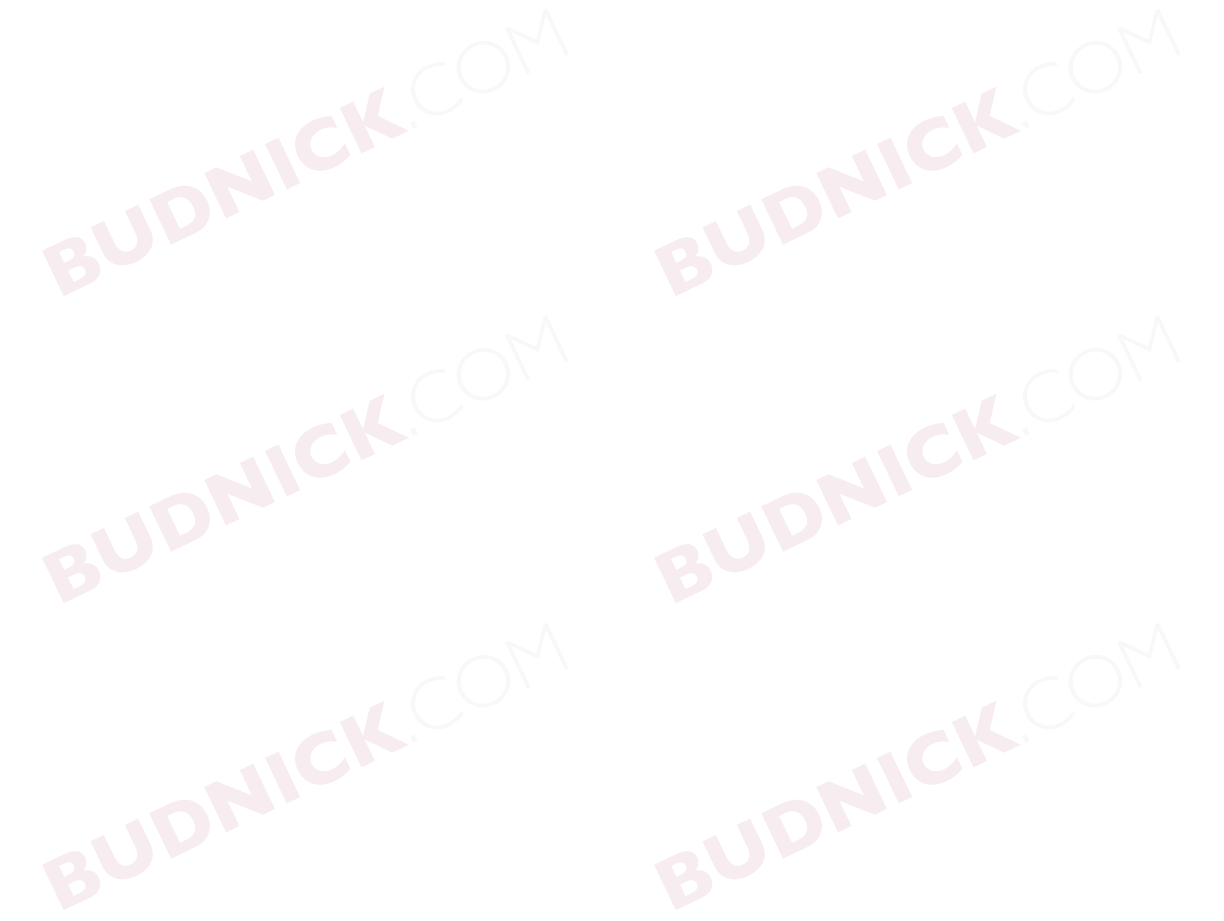
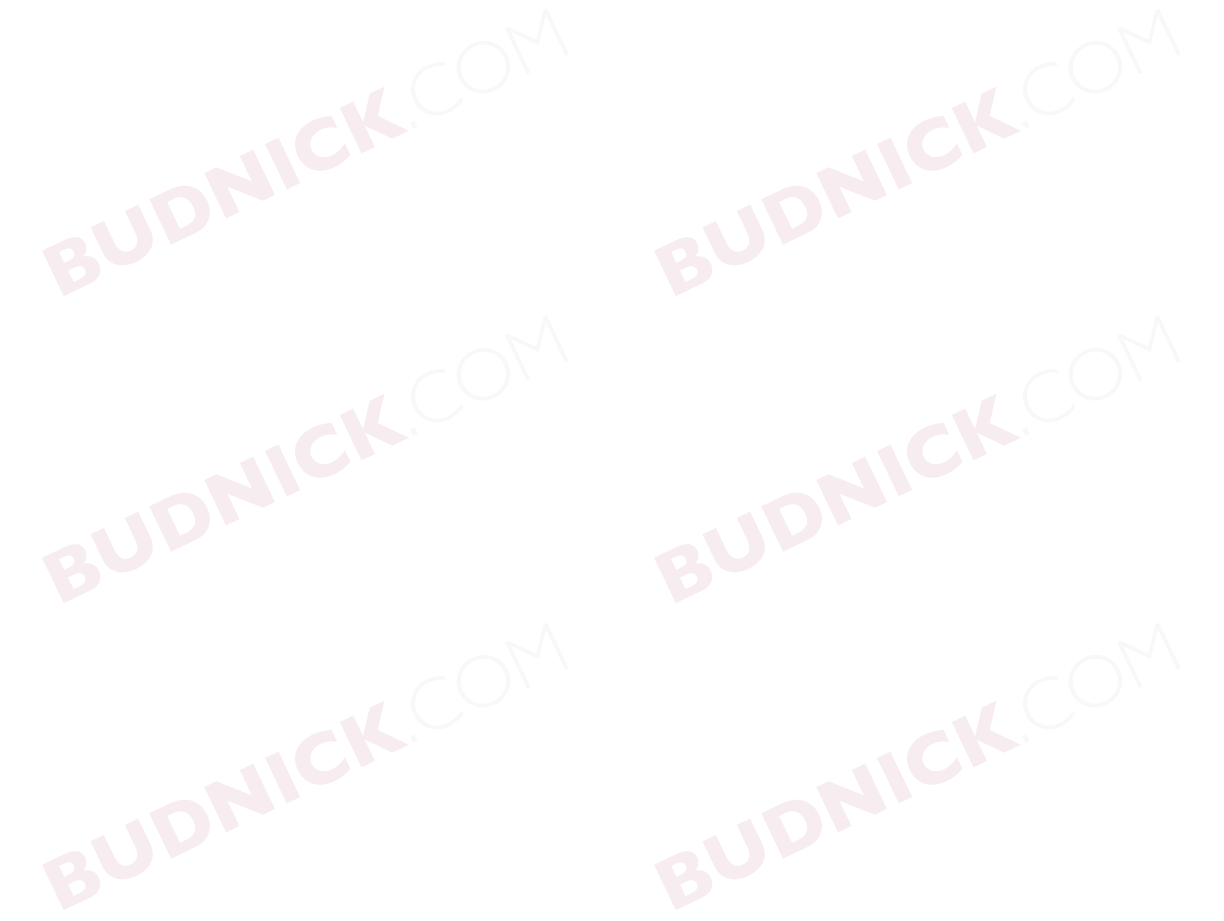
Tape101
One of the biggest missteps you can make in your adhesive selection process is assuming that all tapes are the same - which is why we're here to help you understand the differences.
Get the eBook
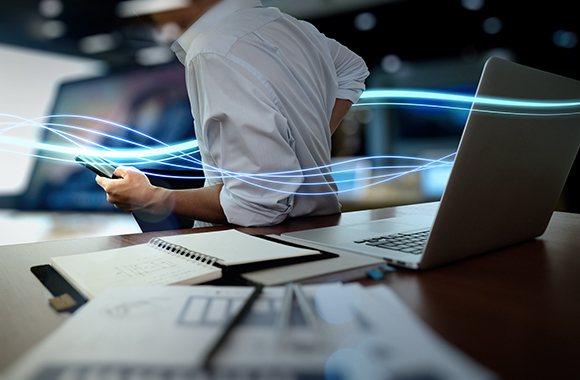
One of the biggest missteps you can make in your adhesive selection process is assuming that all tapes are the same. So much goes into whether an adhesive will work for your specific application, and you should consider each factor when picking out an ideal product. It's important to match the properties of your adhesive to the needs of what you're bonding.
At Budnick.com we've always made it our primary goal to educate our customers as best we can, and our Tape101 eBook and learning center is the next step in that process. We've outlined the basic steps to follow and questions to ask throughout the process of identifying an adhesive so you can approach each project with the knowledge you need to make the best decisions. Feel free to browse through the basics of tapes, or for a more in-depth overview, download our free eBook here!
Case Studies
Budnick has decades of experience developing application, product, and process solutions - read about some of our favorite solutions below!

Case Study Oven Door Assembly
Using an expensive multi-layered double coated foam for gap filling in their oven doors was creating problems for a major appliance manufacturer.
- Developed a better solution with a custom product that fully fit their needs
- Improved the customer's application methods in the process
- Helped both the customer's bottom line and their production line workers
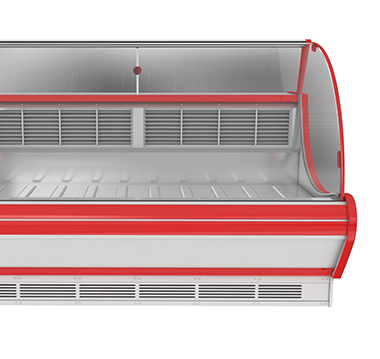
Case Study Small Changes
A customer was using a high tack adhesive for numerous applications throughout their process - but there were issues with some having exposed adhesive.
- Multi-use tape was used for several applications and redundant on use
- After the tape was applied, adhesive was exposed in some areas
- Customer continued with a single product that would fit all the existing applications
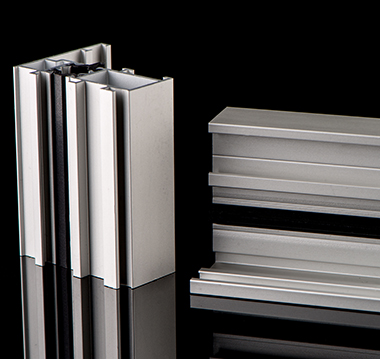
Case Study Efficiency
Working in tandem with our distribution customer, we were able to identify an ideal solution for the end user, improving both production efficiency and the bottom line.
- Distributor approached Budnick regarding their customer, a vinyl window manufacturer
- By modifying the final format we were able to reduce machine stoppage dramatically
- Several options were presented to consider and implement in their processes