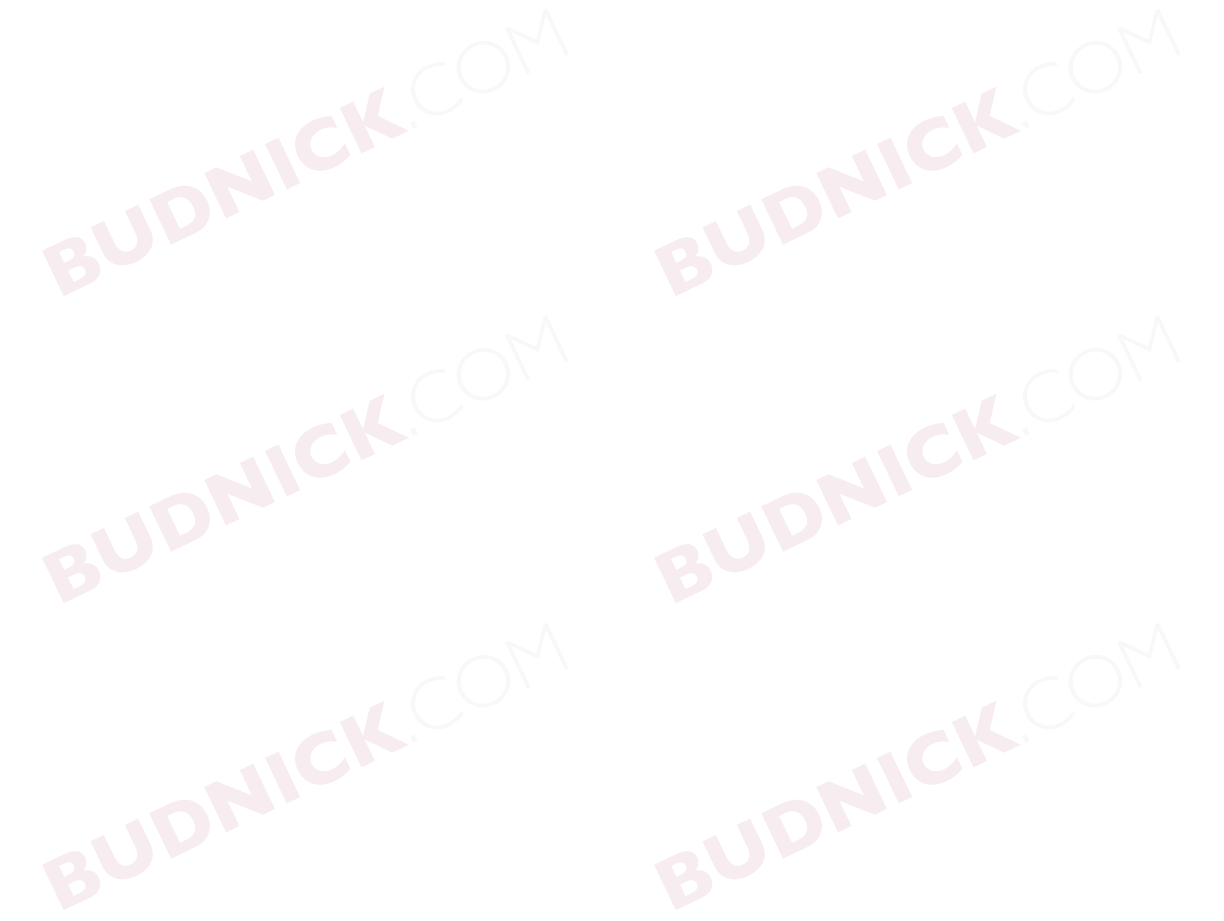
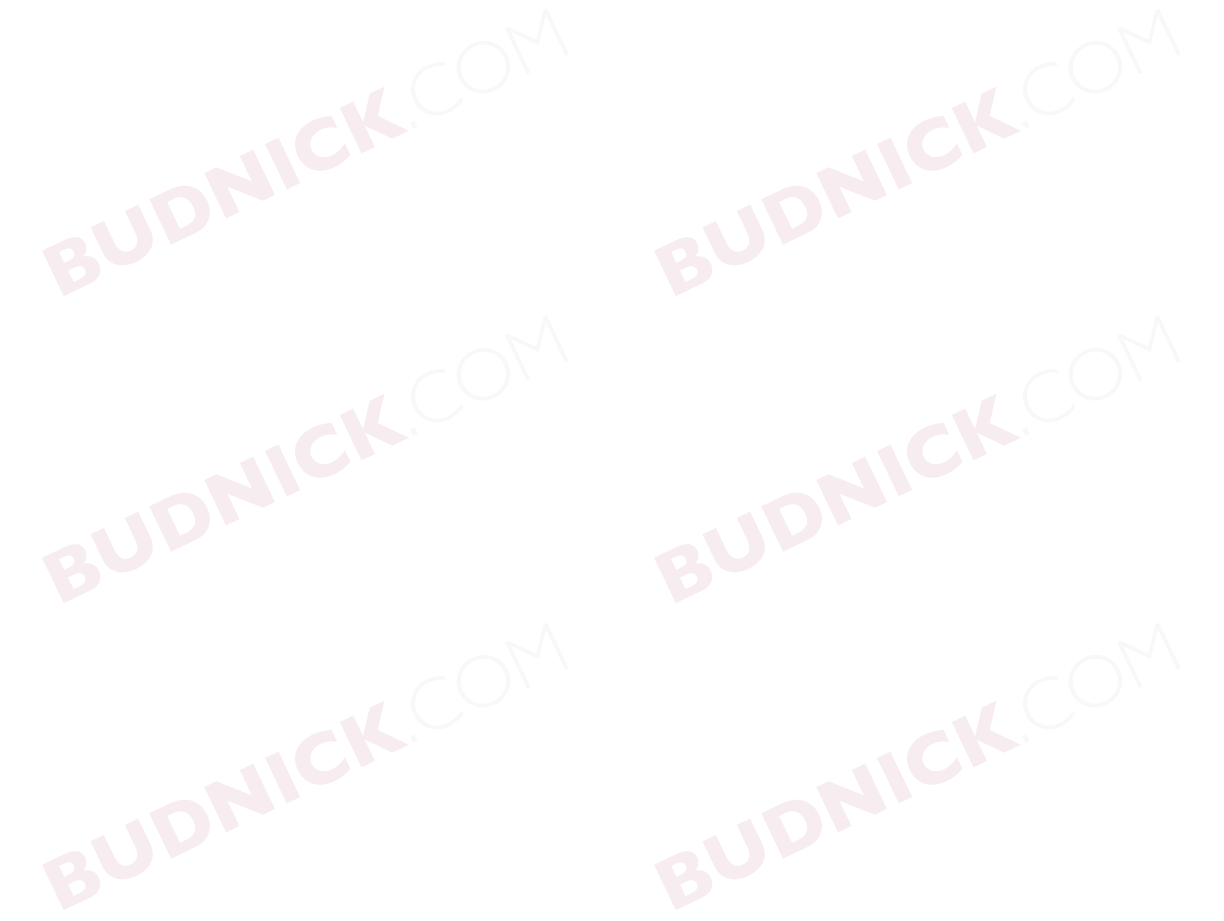
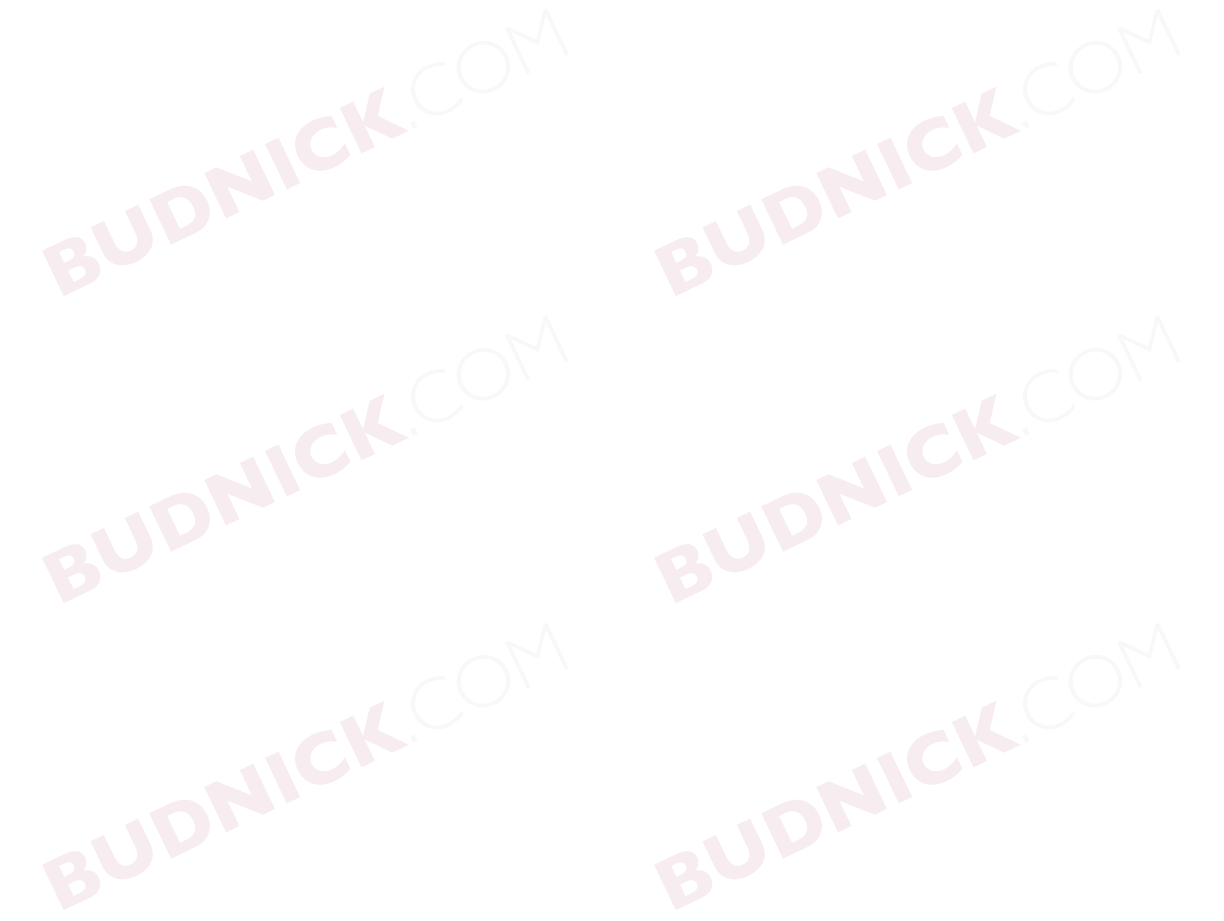
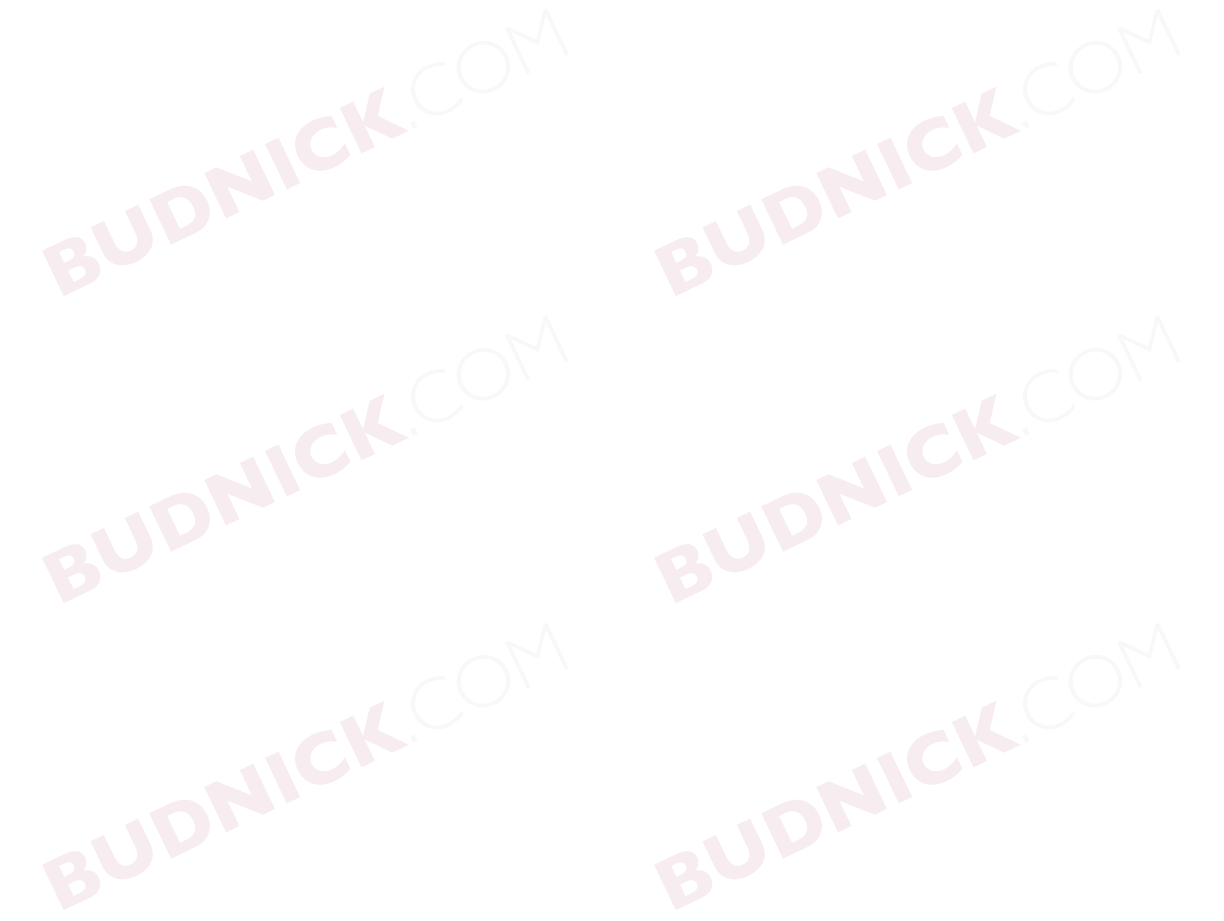
Case Study - Oven Door Assembly
Customer Need
Our customer, an appliance manufacturer, was using an expensive double coated foam in an oven door assembly as a gap filler. Their previous supplier was stacking two of the double coated tapes together that were separated by aluminum foil. This method was somewhat useful, but was not the right thickness. Additionally, there were issues with the foam parts merging back together on the rolls after having been cut.
The Budnick Solution
We collaborated with one of our vendors and began testing a high bond, acrylic foam tape. The appliance manufacturer’s engineers were intrigued when they learned the foam tape could be designed to a particular thickness, prompting our vendor to design a 140 mil thick product.
The new high bond acrylic core product was then butt cut on a press. To reduce waste we were able to create a 1/16’’ gap between the parts on the roll to prevent them from merging back together. Today we provide over 800 parts per roll to the customer. We sell them in roll form as a convenience to the customer’s inventory system.
Enhanced Productivity
The production workers no longer struggle with parts sticking together and breaking. The parts also come presented double linered. The workers prefer this, as they top release liner is removed, exposing the adhesive on multiple parts. As a result, production times have improved, part costs are reduced, and the gap is sufficiently filled in the oven door.