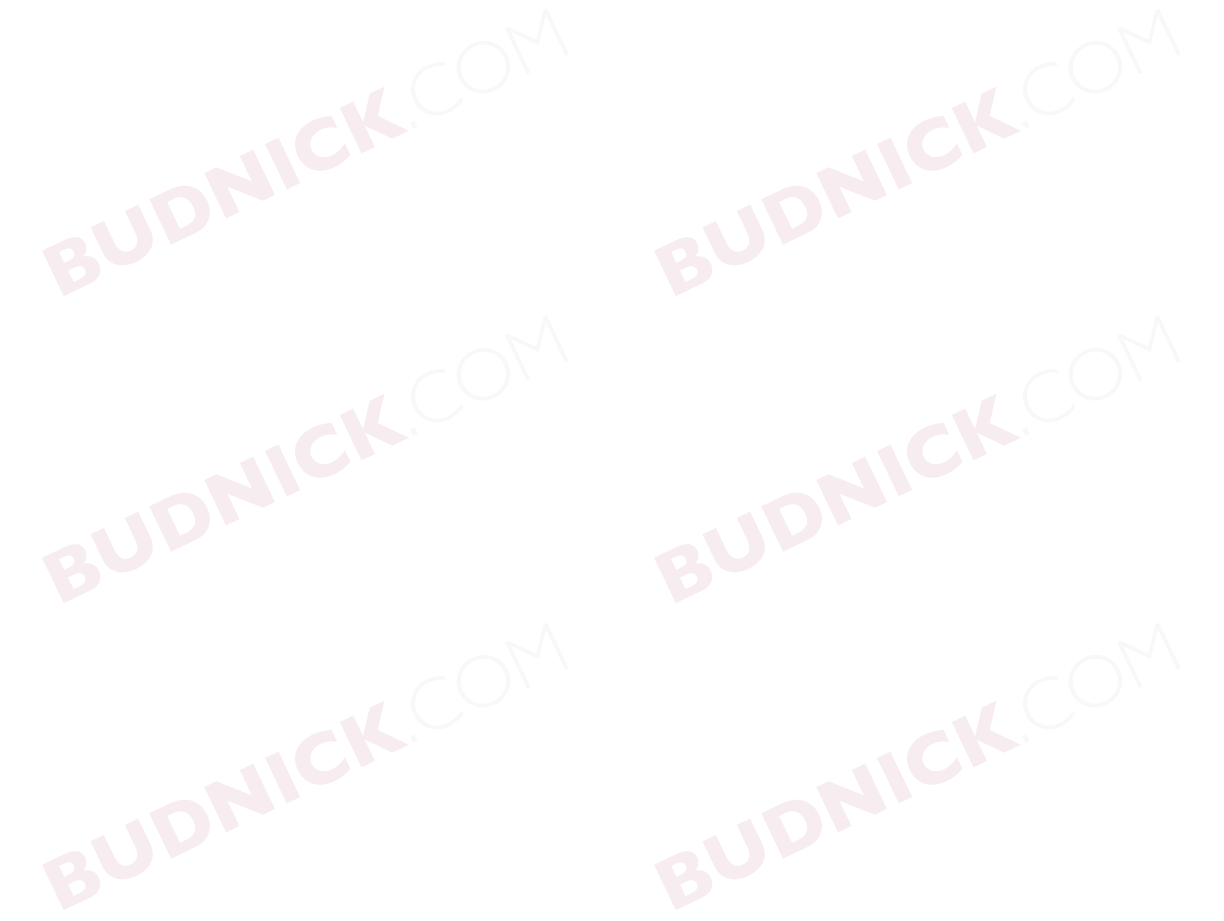
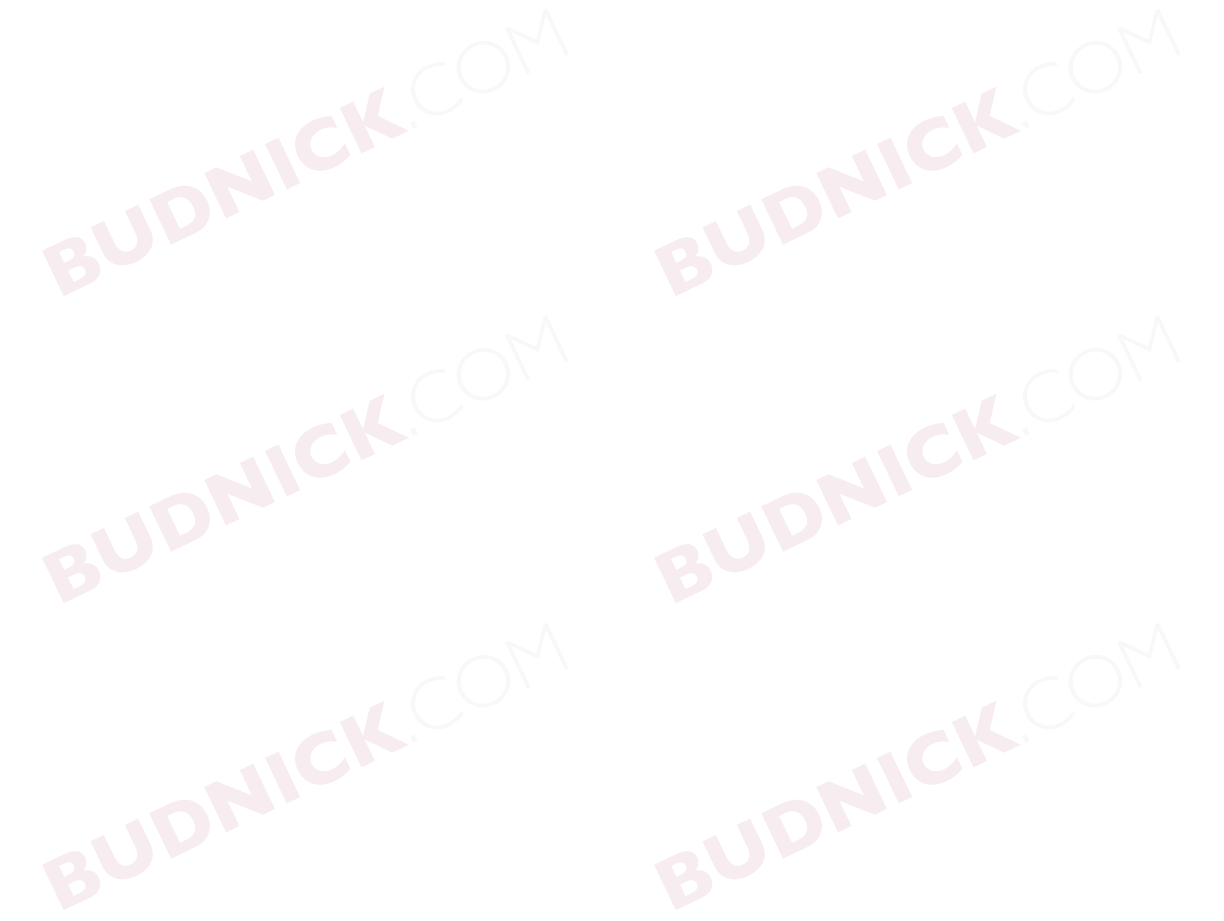
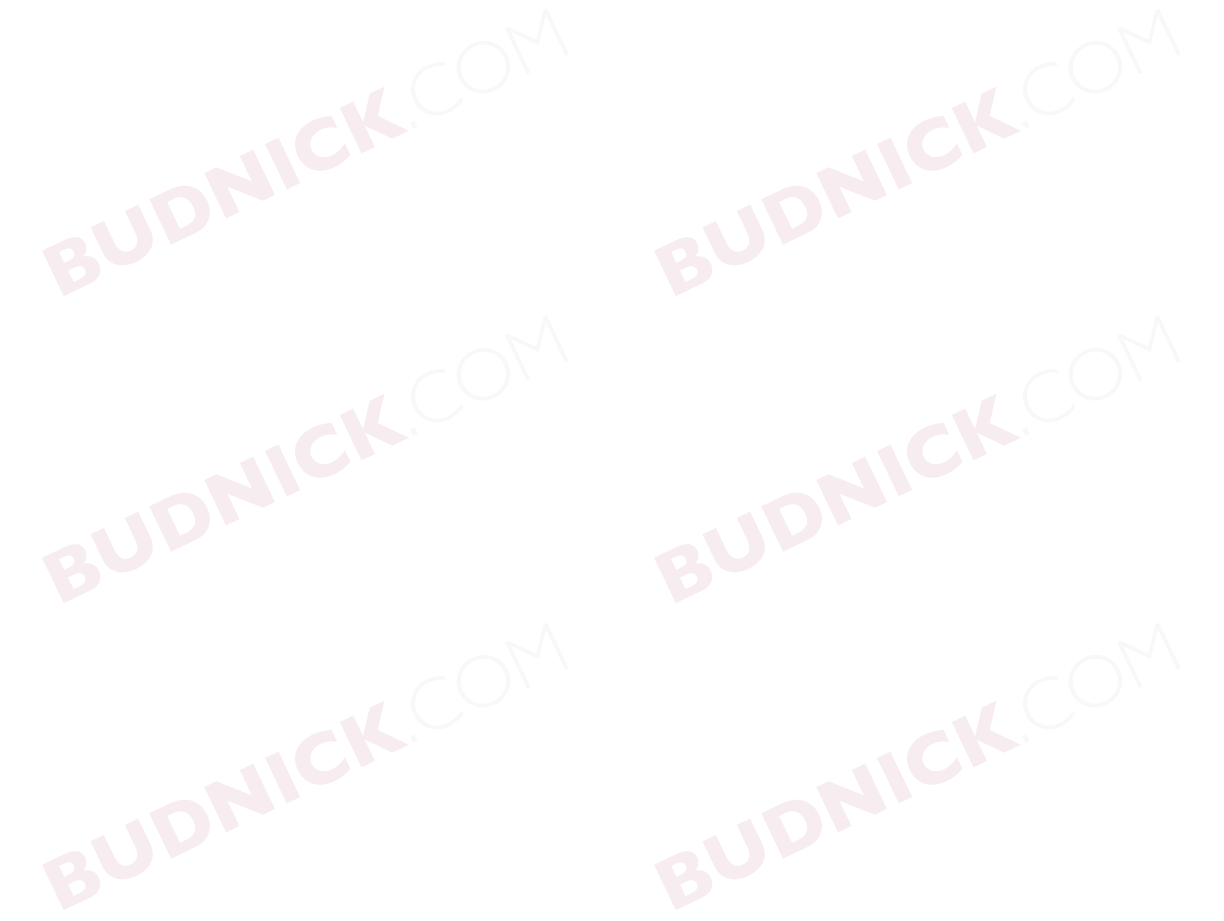
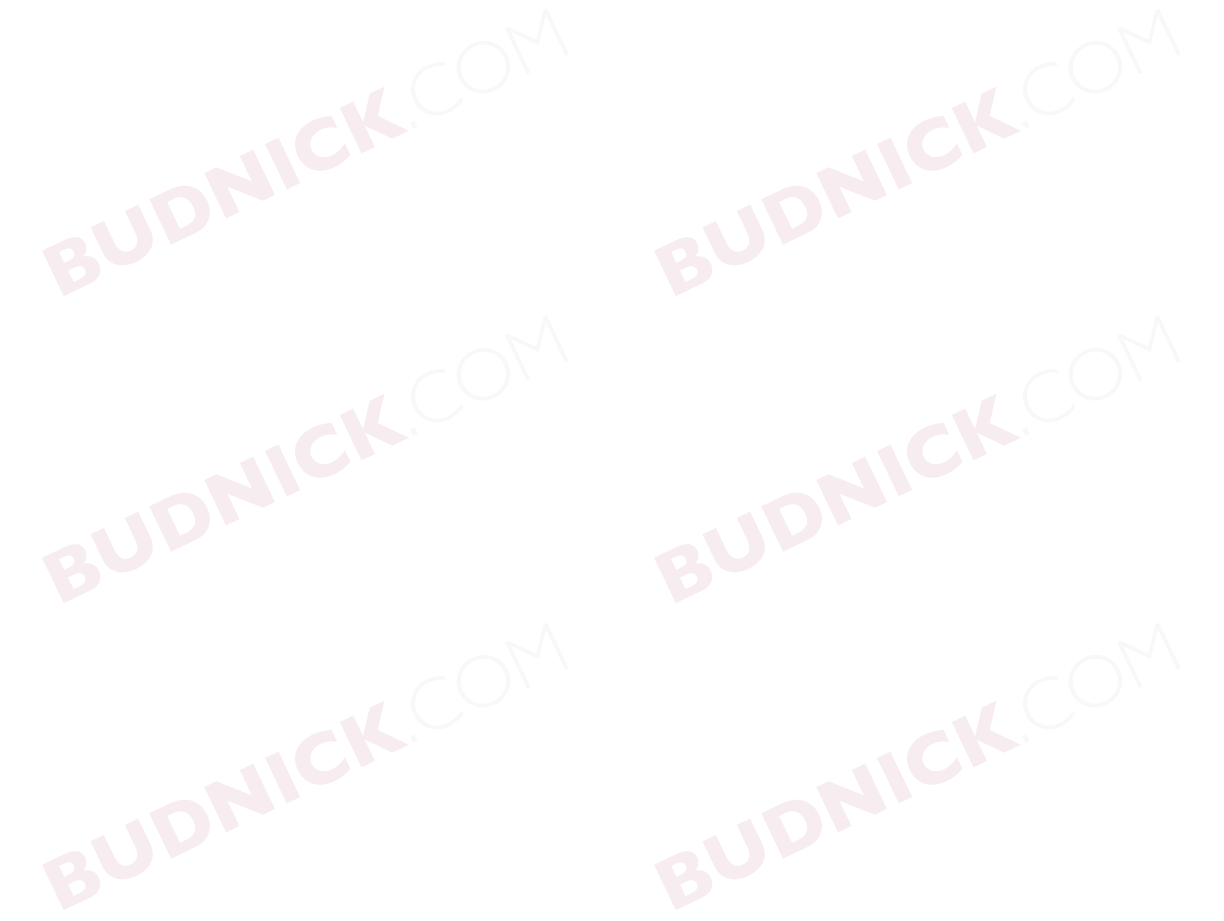
In-Line Laser Cutting
What are the benefits of in-line laser cutting?
No tooling required
Computer Numerically Controlled (CNC) processing means parts can be created from your drawings or computer files.
No design limitations
Laser cutting overcomes the limitations of mechanical tooling. This allows design engineers the freedom to specify part dimensions that optimize finished goods.
Quality parts
The high-speed motion system manipulates the laser beam at a rate of 200 inches/second to cut parts to your desired dimension while processing material at speeds up to 100 feet/minute. This process keeps specialty part costs down and helps meet both prototype and full scale production requirements.
A variety of part dimensions on the same roll
In-line laser processing provides you with a variety of parts on the same roll or sheet. If you require a variety of die-cuts for a single unit, they can all be supplied right next to each other.
Eliminate adhesive flow
Many of today's specialty fastening adhesives tend to flow (bond back to itself) after traditional die-cutting. Laser cutting actually vaporizes the kerf where mechanical die-cutting only displaces the substrate. By vaporizing material, laser cutting prevents cut parts from bonding back to themselves when matrices (scrap material) are left with the finished product. In-line laser procedures also allow matrix removal on many materials that were once inseparable. By removing surrounding scrap material from your finished parts, productivity can be increased with automated application processes.
To learn more about in-line laser cutting, visit BudnickConverting.com
No tooling required
Computer Numerically Controlled (CNC) processing means parts can be created from your drawings or computer files.
No design limitations
Laser cutting overcomes the limitations of mechanical tooling. This allows design engineers the freedom to specify part dimensions that optimize finished goods.
Quality parts
The high-speed motion system manipulates the laser beam at a rate of 200 inches/second to cut parts to your desired dimension while processing material at speeds up to 100 feet/minute. This process keeps specialty part costs down and helps meet both prototype and full scale production requirements.
A variety of part dimensions on the same roll
In-line laser processing provides you with a variety of parts on the same roll or sheet. If you require a variety of die-cuts for a single unit, they can all be supplied right next to each other.
Eliminate adhesive flow
Many of today's specialty fastening adhesives tend to flow (bond back to itself) after traditional die-cutting. Laser cutting actually vaporizes the kerf where mechanical die-cutting only displaces the substrate. By vaporizing material, laser cutting prevents cut parts from bonding back to themselves when matrices (scrap material) are left with the finished product. In-line laser procedures also allow matrix removal on many materials that were once inseparable. By removing surrounding scrap material from your finished parts, productivity can be increased with automated application processes.
To learn more about in-line laser cutting, visit BudnickConverting.com