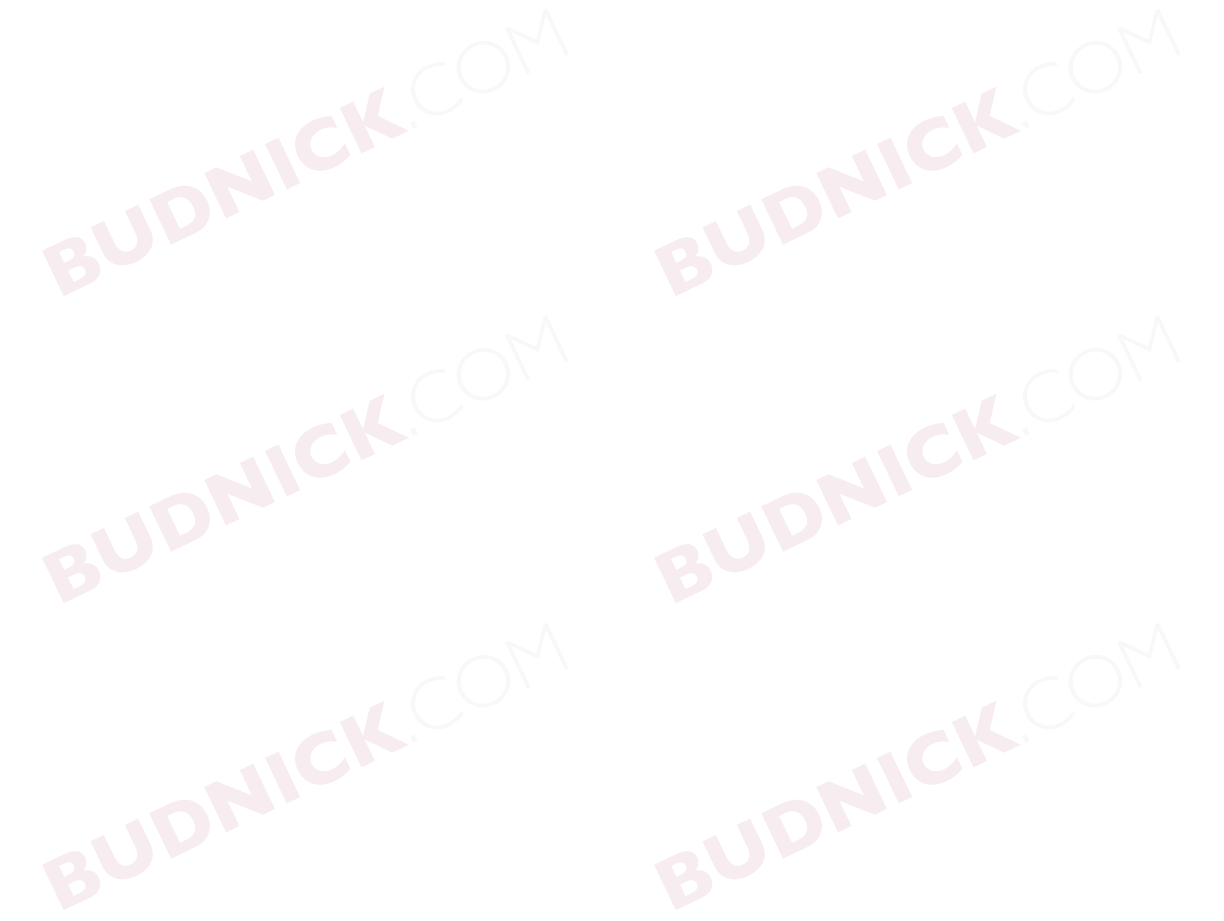
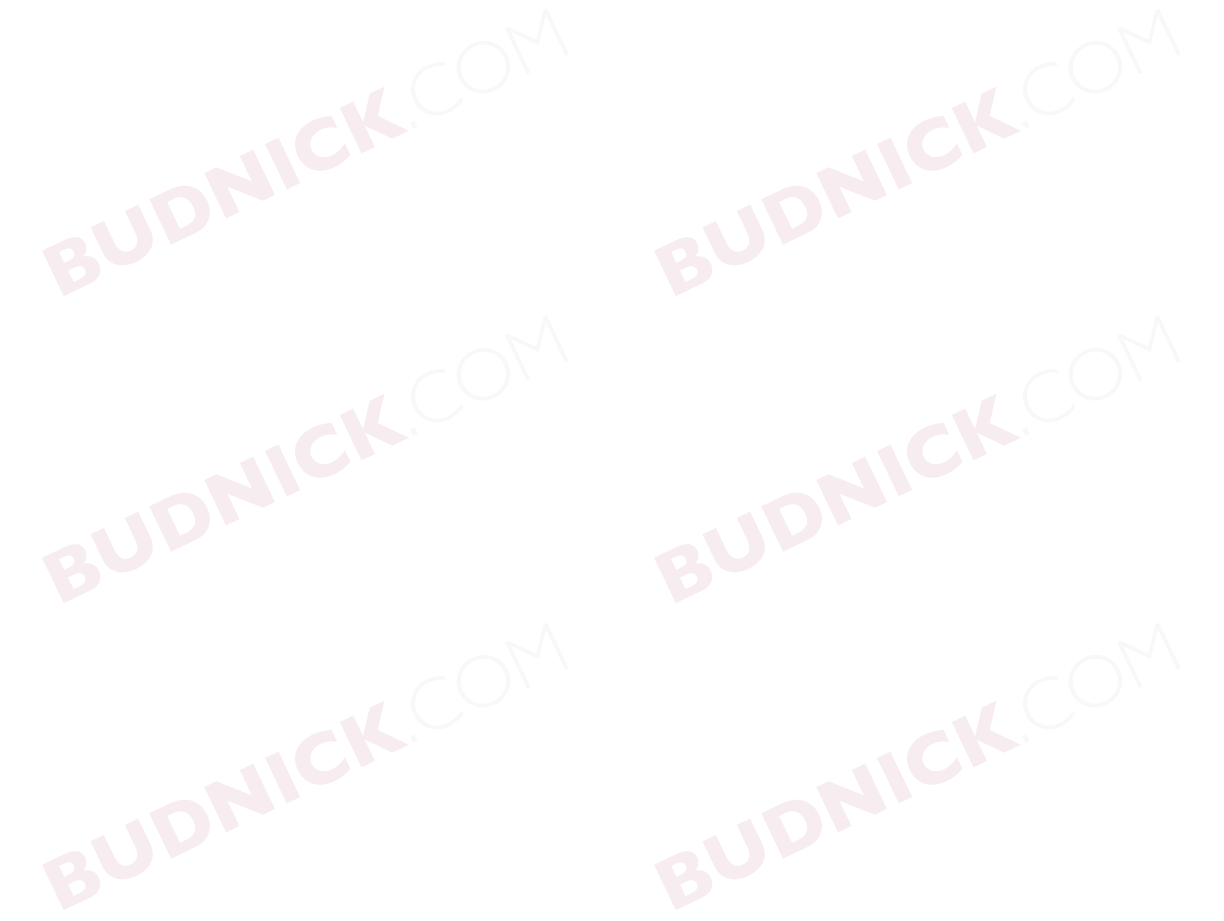
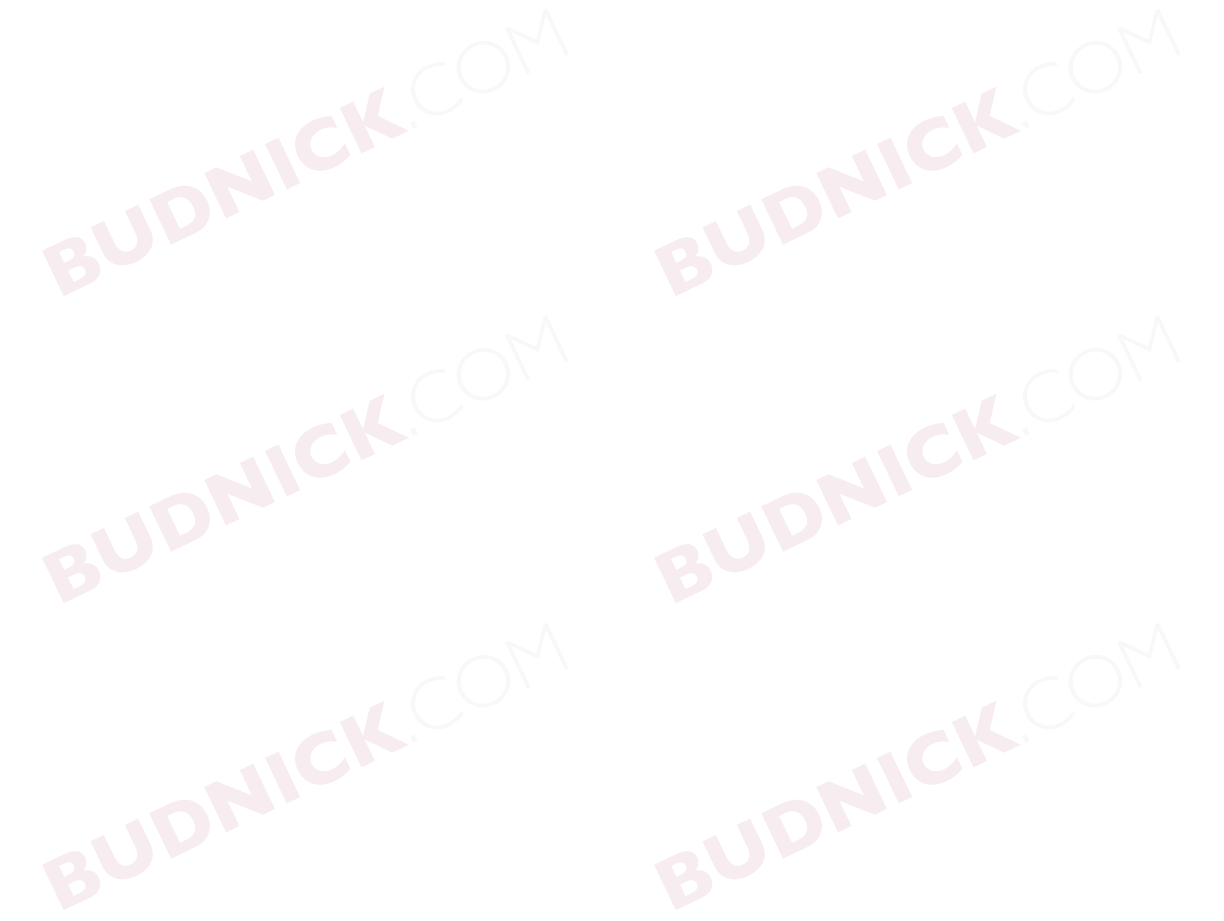
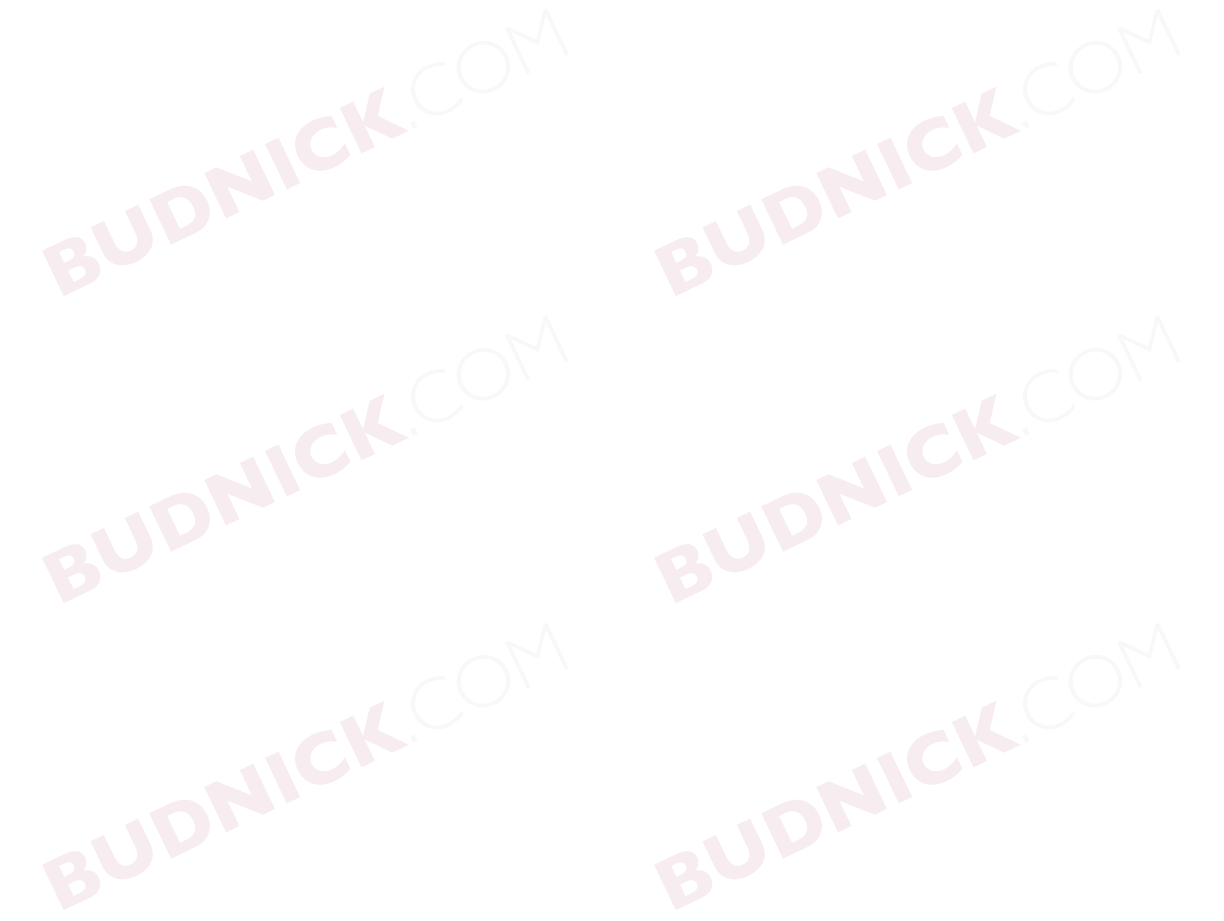
Meeting Six Challenges of Lightweighting
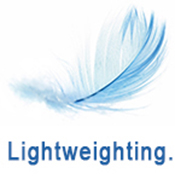
The design requirement for lightweighting of products is generally driven by at least one of the following mandates: 1) reduce product energy consumption; 2) decrease manufacturing costs; or 3) reduce size to improve portability, aesthetics and/or user convenience. However, when implementing lightweighting, design engineers frequently encounter several of the following six challenges.
- Adhesion to lighter weight substrates
Substrates such as metal and plastic can have significantly different physical and chemical properties that must be accommodated in new, lighter weight designs. Generally, with each decrease in substrate weight, adhesion to the lighter substrate becomes more difficult. For example, when changing from steel to aluminum in light duty trailers; from aluminum to engineering plastic in small appliances, handheld tools or consumer electronics; or from engineering plastic to polyethylene or propylene (PE/PP) in appliance control panel housings. While adhesion to a lighter weight material may not be achievable with the adhesive previously used on a heavier material, a range of 3M adhesion solutions are available for each materials category.
- Attaching dissimilar substrates
Attaching two pieces of the same substrate, such as steel to steel, is not problematic. However, joining dissimilar substrates can be formidable due to the differences in their chemical properties. For instance, if steel and aluminum are directly attached, an electrochemical reaction will occur and cause corrosion of the metals. Still, light duty trailers can be changed from all-steel construction to steel panels with aluminum posts by using 3M™ VHB™ Tape, which can provide both separation of substrates and adhesion.
- Noisier substrates
Lighter weight substrates can produce more vibration, which creates noise of greater frequency (i.e., more vibrations per second) and/or higher pitch (i.e., more soprano in tone). In turn, these can create perceptions of lower quality or decreased safety, for example, in the doors of commercial vehicles. However, materials from 3M can be used to provide sound damping, thereby decreasing excessive frequency and pitch and improving a user's view of product quality.
- Weaker, more flexible substrates
Lighter weight substrates can be more flexible but weaker, so some products may need reinforcement to increase product strength. However, reinforcing materials must be light-weight enough to provide a net reduction in product weight. 3M adhesion technology can be used to achieve this in a variety of applications such as small appliances, handheld tools, electronics and signage.
- Heat and flame susceptibility of substrates
Heat and flame resistance are critical considerations in designing products as diverse as hair dryers, vacuums, snowmobiles and commercial vehicle battery cables. Some applications may require overall heat resistance while others need one-time protection from a flame event at the end of product life. When lightweighting, if a new substrate is susceptible to heat or flame, 3M foil tapes can provide the necessary protection.
- Visual appearance of substrates
Changing to lighter weight substrates, especially from metal to plastic, can significantly change the appearance of products and create the perception of reduced quality. However, this can be addressed by adding veneers to new substrates or products to enhance their aesthetics and consumer appeal. Adhesion solutions from 3M can be used on products such as consumer electronics or large home appliances to make plastic surfaces more appealing or make them appear to be metal.