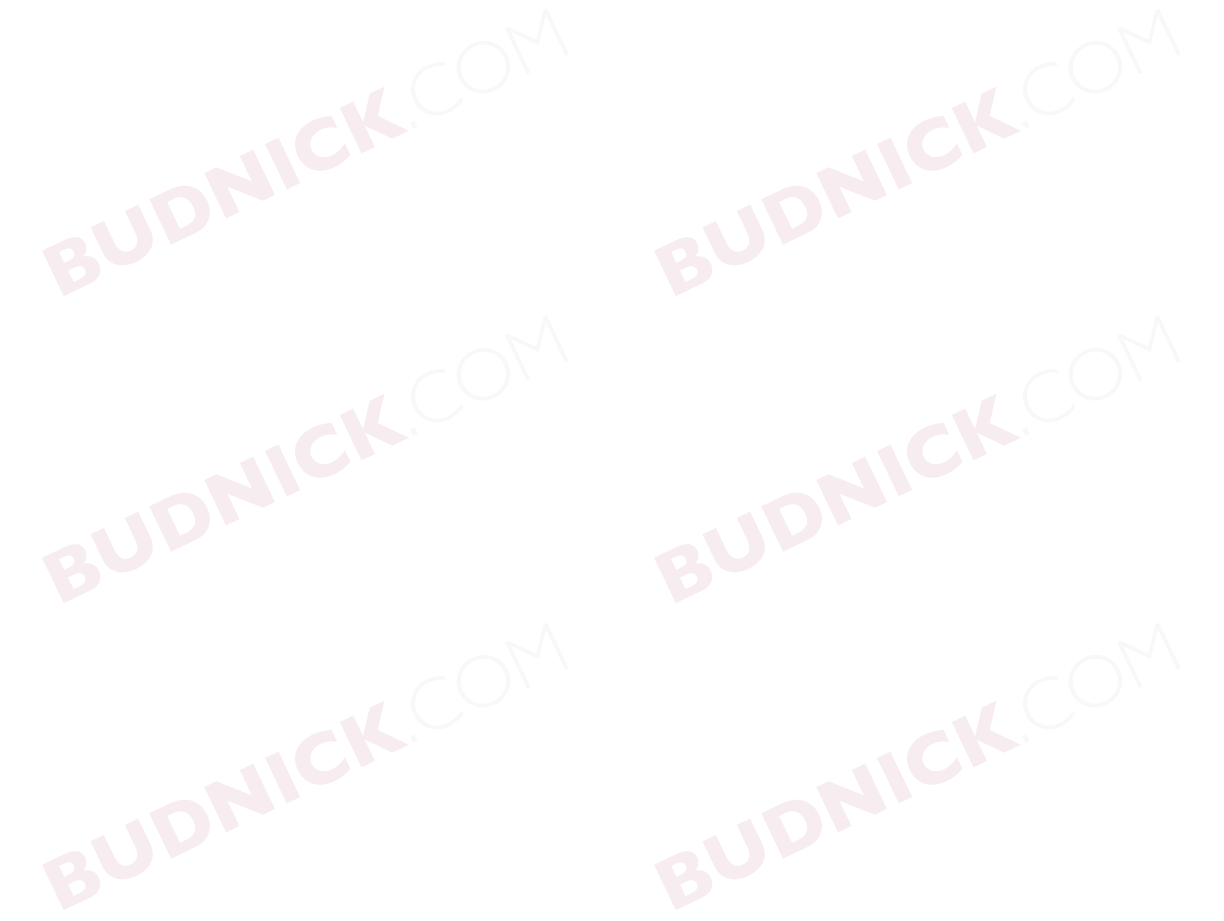
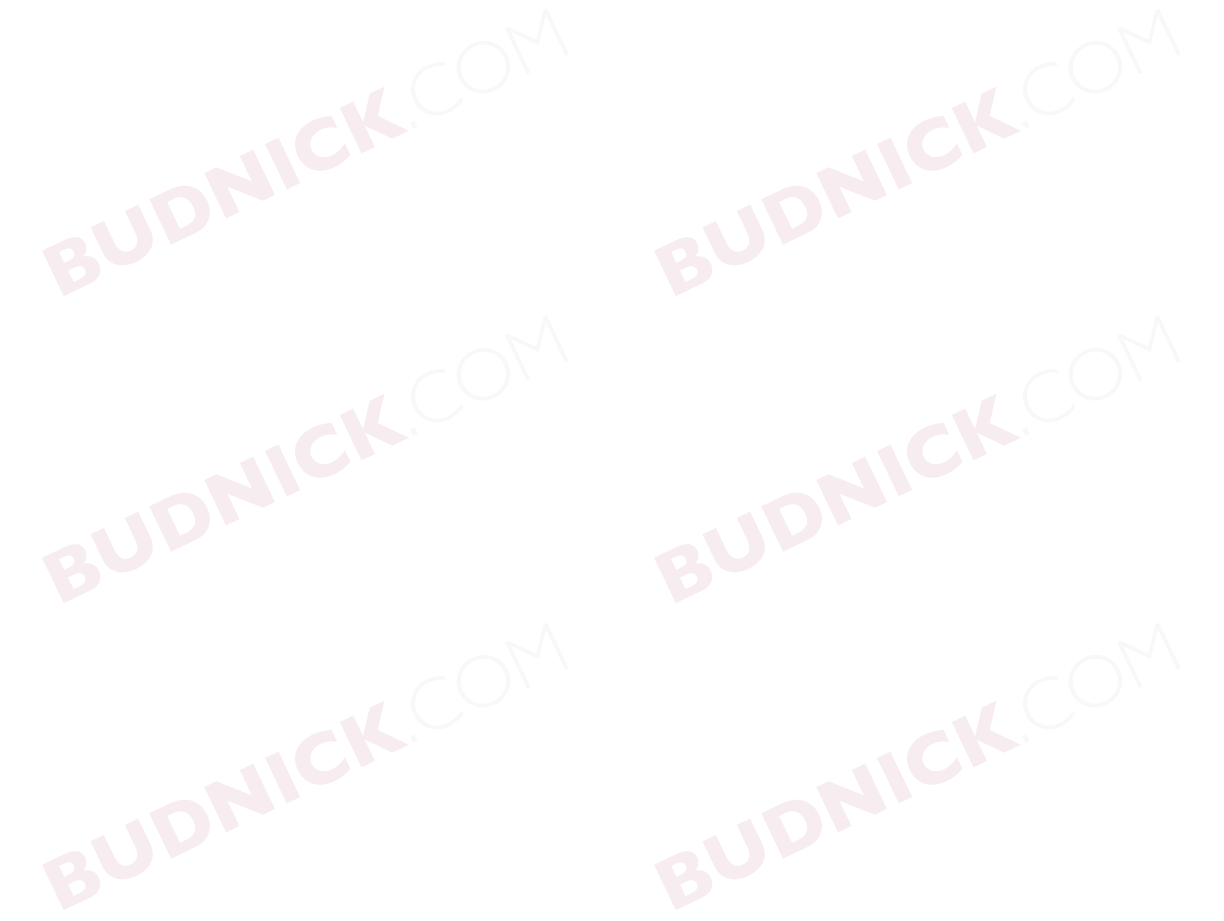
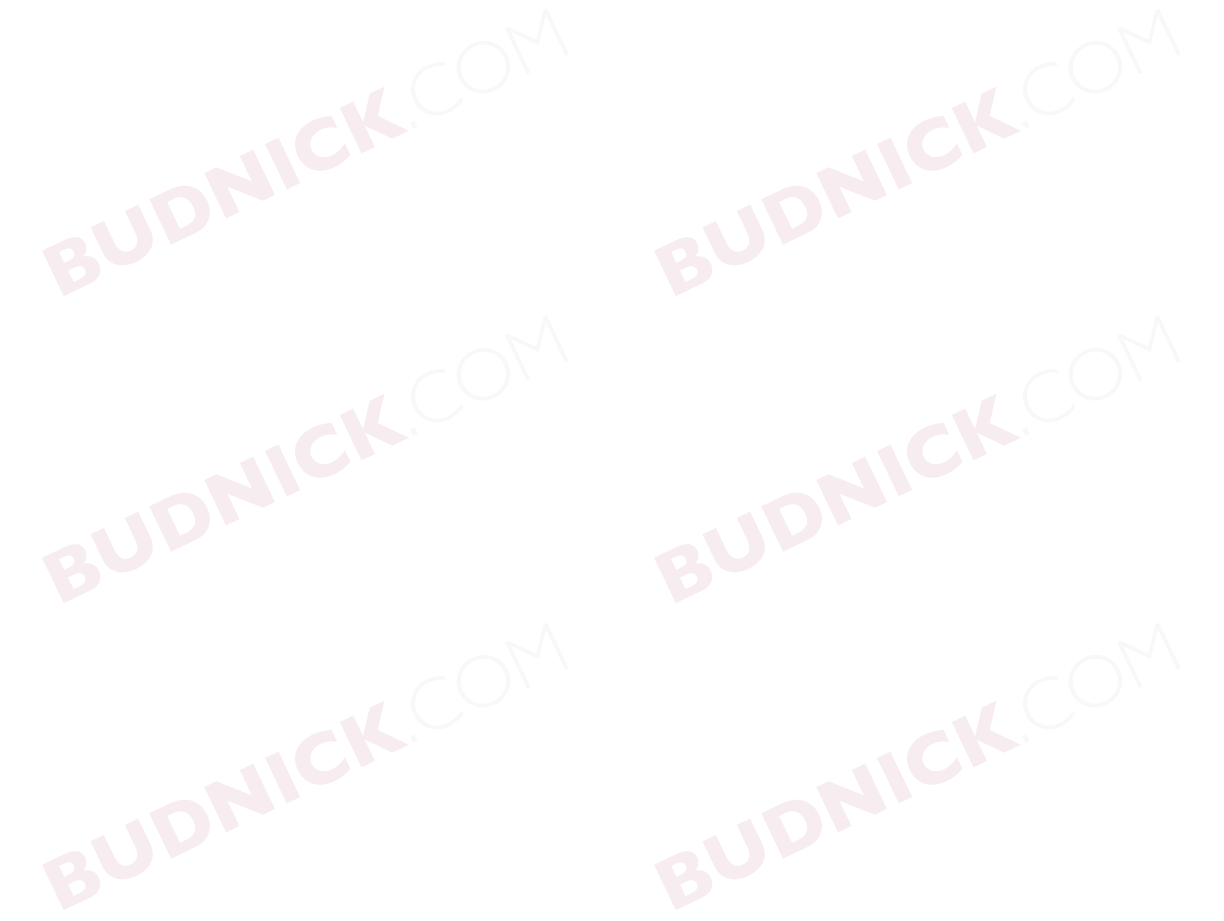
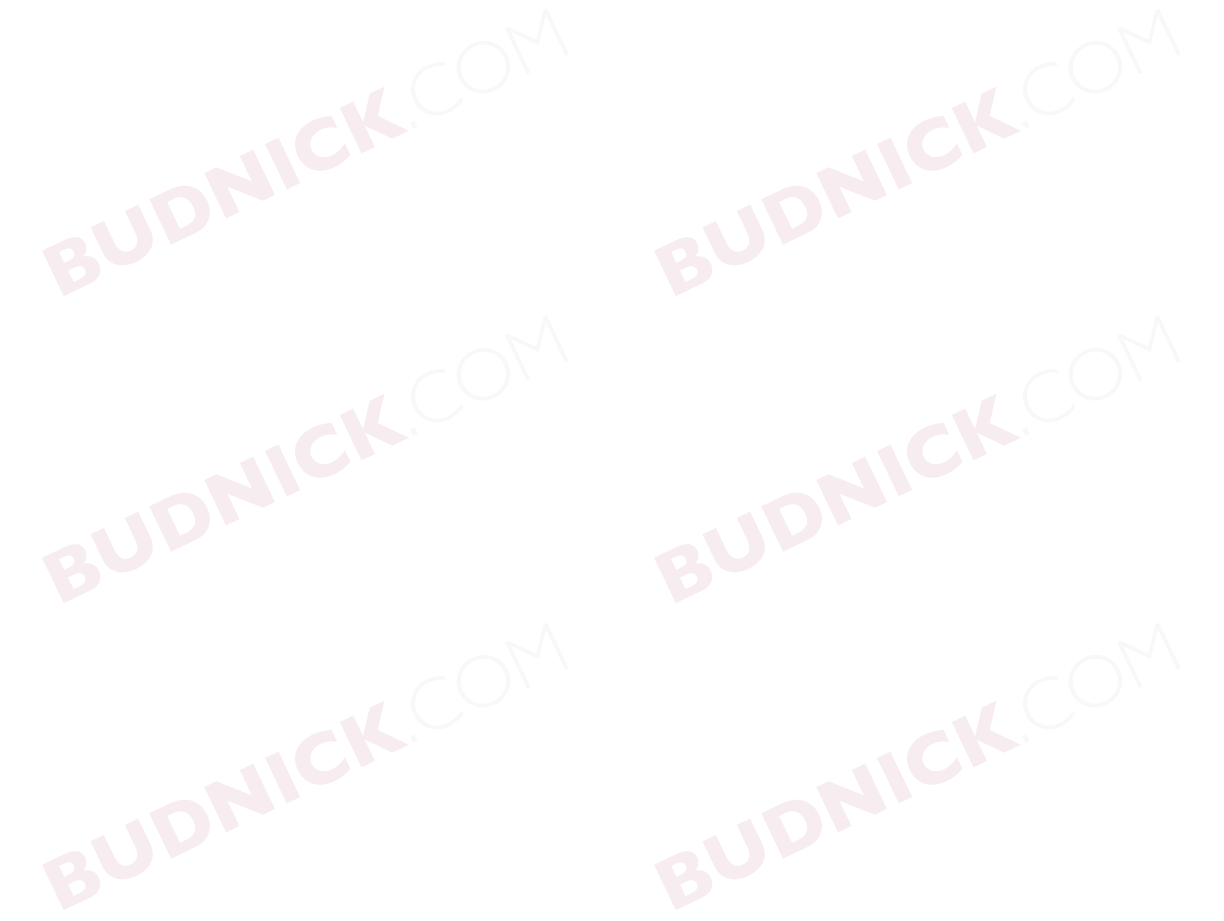
Pro Tips for Surface Preparation and Priming to Get the Best Bond
In most instances, a bonding tape can be selected that bonds well enough to the substrates to meet the needs of the application. However, you should always consider the surface and environment that you are working with.
Before bonding, surfaces should be clean, dry, unified and free of wax, oils, dust and other contaminates. Some typical surface cleaning solvents are a 50/50 isopropyl alcohol and water mixture or heptane. Light abrasion can be used to remove lose materials or other contaminations from the surface and should be followed by thorough cleaning.
When dealing with difficult to bond substrates and critical applications, use of an adhesion promoter or primer can increase adhesion levels and help ensure the best ultimate bond strength. 3M Adhesion Promoter 111 (AP-111) and 3M Primer 94 (P94) are two broadly useful promoters for high strength bonding tapes and form the basis for an easy primer selection system.
When a primer is needed, 3M AP-111 is often a preferred choice because it is isopropyl alcohol based and is quick and easy to use on a variety of surfaces. In some cases, it can be used as a cleaner and primer in one step. This promoter is typically applied by putting on a tissue or clean rag and then wiping the surface in a cleaning motion, followed by wiping any remaining material on the surface dry. The surface is ready for bonding immediately after application assuming the surface is dry.
For 3M Primer 94 and other similar resin based promoters application is typically done by brush, felt tip applicator or similar method. After application, the primer must be allowed to dry, possibly up to 5 minutes depending on air flow and temperature.
3M Adhesion Promoter 111 is generally a first choice for painted surfaces and bare metals. This promoter works on a wide variety of paints and bare metals, the primary exception is textured paints and rough metals where effectiveness can be lower. If the paint surface is relatively clean, consider evaluation of the promoter as a cleaner and primer in one step. For bare metals, cleaning the metal prior to use of the promoter is suggested as any contamination typically found on the metal can interfere with the promoter’s effectiveness.
3M Primer 94 is generally a first choice for plastics, including many low surface energy plastics, and rubber materials. This primer system is somewhat universal in nature and also works on a variety of paint and bare metal surfaces.
While AP-111 is not a first choice broadly for plastics, it has been found to work well on many smooth, hard medium to high surface energy plastics such as: polyester, polycarbonate, acrylic and Nylon®. Many times a promoter is not needed on these materials, but AP-111 can be considered as an option as a cleaner/primer if higher strength is desired.
Below is a quick outline of primer selection by substrate:
Substrate Material: | First Choice | Alternate |
Bare Metal | AP-111 | P94 |
Paint and Painted Metal | AP-111 | P94 |
High and Medium Surface Energy Plastics | P94 | AP-111 |
Low Surface Energy Plastics | P94 | |
Rubber | P94 |
***NOTE***
Please be sure to obtain a copy of the product information bulletin and material safety data sheets for each of these adhesion promoters and follow all instructions. Because substrate materials can vary it is important to evaluate the primer on the specific substrate to be used to insure it has good bond strength and meets the total needs of the application. Alternate primers are available for situations where AP-111 and P94 are not suitable, and alternate application techniques can be considered for extremely hard to bond substrates.
To select the proper adhesive tape, carefully evaluate all application variables, seek assistance from industry professionals and perform thorough testing. For best results, remember that most tapes should be applied with pressure and at temperatures between 50 and 100 degrees F.