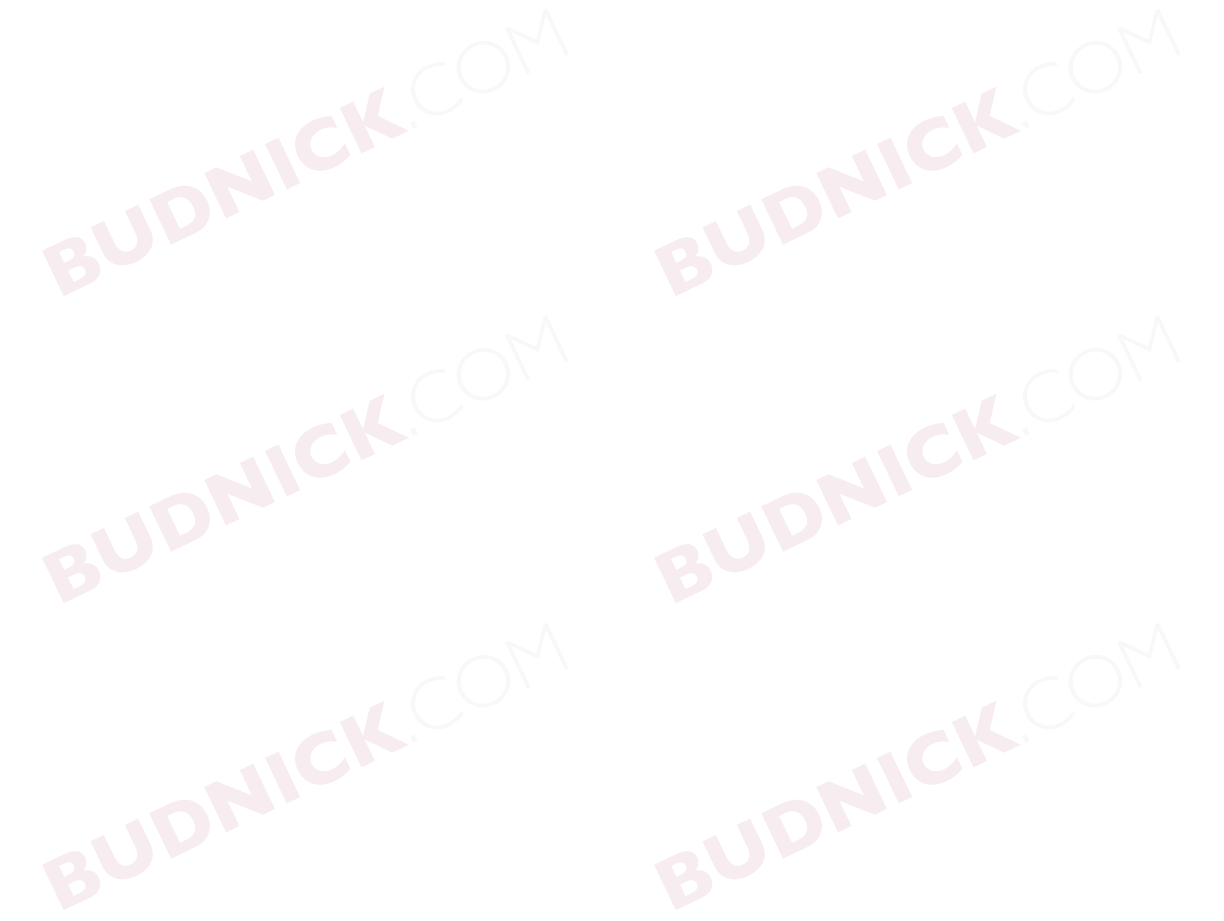
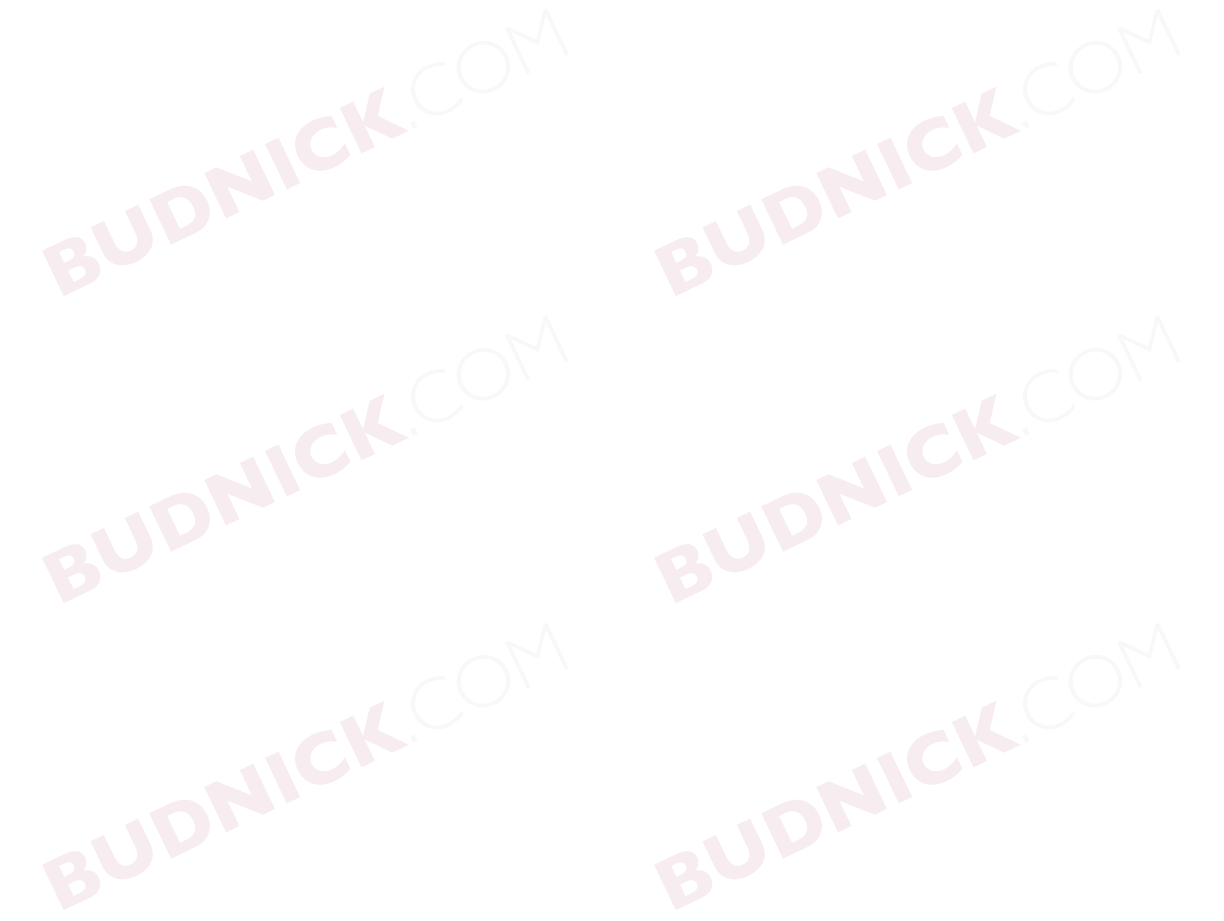
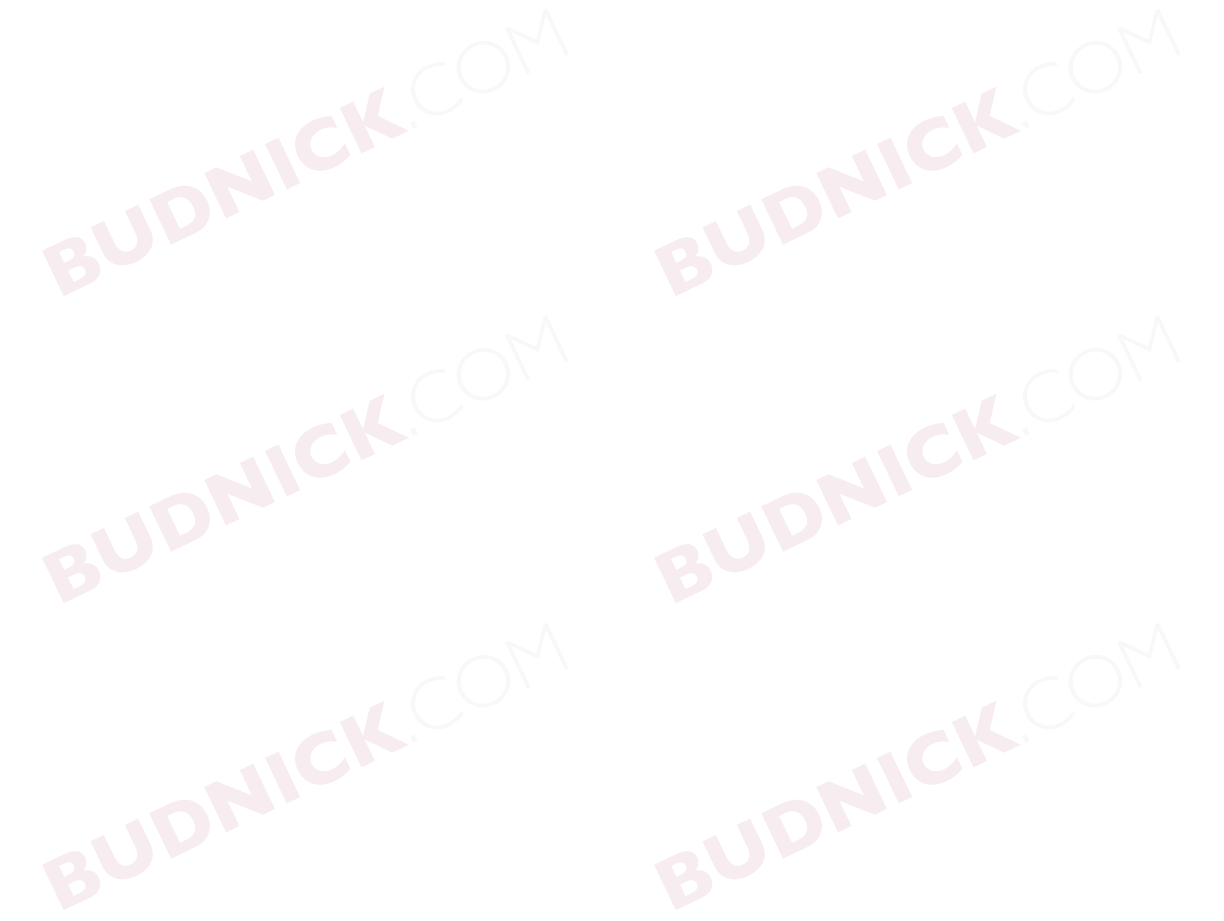
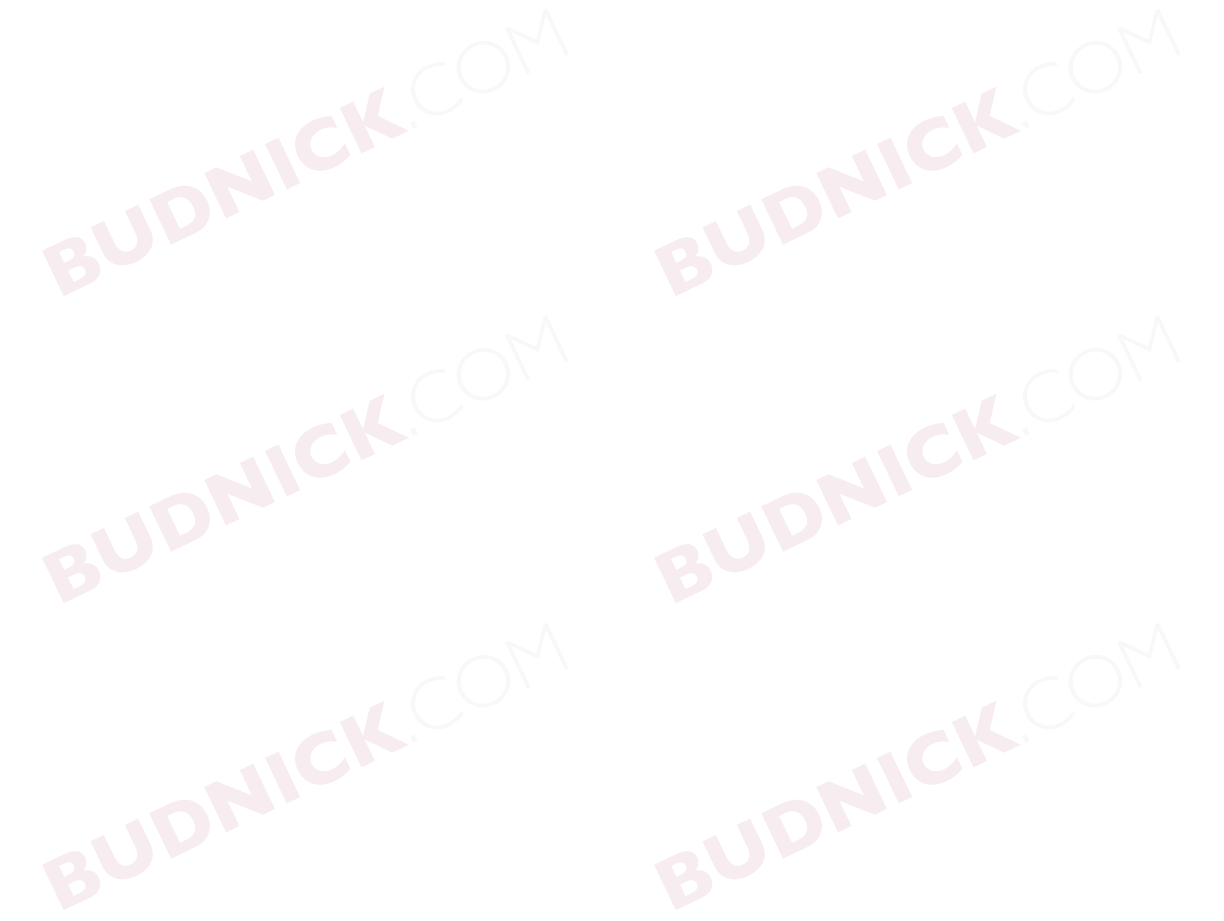
Take the Nuts, Bolts, Rivets, and Glue Out of Bonding Applications
Why Adhesive Tapes Might Be a Better Choice for Select Applications.
In today's industrial manufacturing and construction environments, a variety of both traditional and modern materials, such as composites and plastics, are being utilized to produce finished products and building structures in all shapes, sizes, and configurations. In many instances, a bonding or fastening method is needed to join two or more components to product the end product or to affix one product to another. While traditional fastening mechanisms such as nuts and bolts, rivets, nails, and glues might come to mind initially, a closer look at pressure-sensitive adhesive tapes (PSAs) reveals the benefits of utilizing adhesive tapes for select permanent fastening and bonding applications.
Compared to Mechanical Fasteners
There is little doubt that mechanical fasteners (nuts, bolts, nails, screws, rivets, and more) "hold" a prominent position in bonding and joining applications in a variety of products, structures, and industries. By their very nature, however, mechanical fasteners can present challenges in design, aesthetics, cost, manufacturing processes, and performance over time.
In the Design Phase
In the design phase, the use of mechanical fasteners requires that the designer choose materials with higher strengths that can withstand the localized stresses at the attachment points for the fastener. This might limit the type of materials that can be used to more expensive or less attractive materials.
Tapes are optimal for joining dissimilar materials for three key reasons:
-
if the two materials are different metals, the tape can act as a barrier to reduce or prevent bimettalic corrosion
-
the materials can expand and contract at different rates over a specific temperature range
-
the viscoelastic nature of PSA tapes can dissipate stress, thus providing for continuous, stable levels of durability
For a "clean design that does not draw the viewer's attention to the fasteners, some mechanical fasteners can be hidden from view, albeit with added cost in materials and processing. Tapes are typically not applied in visible areas, and in some instances, color can be selected to further minimize their appearance in a small gap. Ultimately, the designer has greater freedom to choose materials based on cost, appearance, and weight.
In the Manufacturing Phase
In the manufacturing process, the use of mechanical fasteners often requires holes to be drilled or punctures to be made in the mating materials being fastened. Other joining methods, such as arc or spin welding, may also require additional finishing or high skill with extreme care to achieve a desired appearance.
PSA tapes do not alter the visible surface in any way.
Generally, there are no primary or secondary operations required on the materials to use PSA tapes. PSA tape can be applied by operators by hand or with tools ranging from hand-held dispensers to robots. Operator training to use tape is minimal.
Performance
With regard to reliable and durable performance, the holes created for mechanical fasteners have the potential to reduce the structural integrity of the material. Holes in plastics may cause splitting and crazing.
PSA tapes distribute stresses over a larger surface area compared to mechanical fasteners, thus preventing splitting and crazing.
When a hole is placed in metal, even one treated with corrosion-resistant coatings, the cut edge of the hole becomes a potential site for rust. Moreover, as time progresses and environmental changes occur, such as shifts in temperature and humidity, both materials and mechanical fasteners can expand and contract, creating an opportunity for a loosening of the fastened area. PSA tapes relieve these stresses due to their viscoelastic feature, having the ability to flow and elongate. The PSA tape property of viscoelasticity also compensates for vibrational fatigue to potentially increase joint life as compared to fasteners. Lastly, PSA tapes have been formulated to provide the strength required for the component life based on material, separating stresses, and environmental conditions, such as high and low-temperature exposure, humidity exposure, chemical immersion, and cycles of multiple conditions.
Compared to Glue
Much like mechanical fasteners, industrial strength glues are used for a variety of fastening and bonding applications. While seemingly handy at first glance, all glues present challenges. Unlike fasteners which provide immediate fixation, most adhesives undergo a process of "curing" or "drying." If your component is not immediately secured, them misalignment can occur.
Expensive devices can be used to address this issue. There are fast curing or drying adhesives, but the window to properly align the components is controlled by the adhesive. The equipment to dispense these types of adhesives can also be more difficult to maintain over time. If a slow curing or drying adhesive is used, then additional costs may be incurred to use special equipment to cure/dry the adhesive. By utilizing the properly defined PSA tape, the materials can be immediately secured.
During the assembly process, great care must be used to prevent oozing and overflow of adhesives from the joint onto visible surfaces. The adhesive thickness bust be maintained over the length of the bond or strength could be compromised. Maintaining adhesive thickness may mean adding a stand-off to the component design or an expensive device to maintain the gap until the adhesive is cured.
With PSA tapes, one never has to be concerned with overflowing and dripping adhesive or inconsistent adhesive thickness. PSA tapes also allow for easier repair procedures than cured adhesives.
For more information on the PSA tapes offered by tesa, contact your Budnick representative!